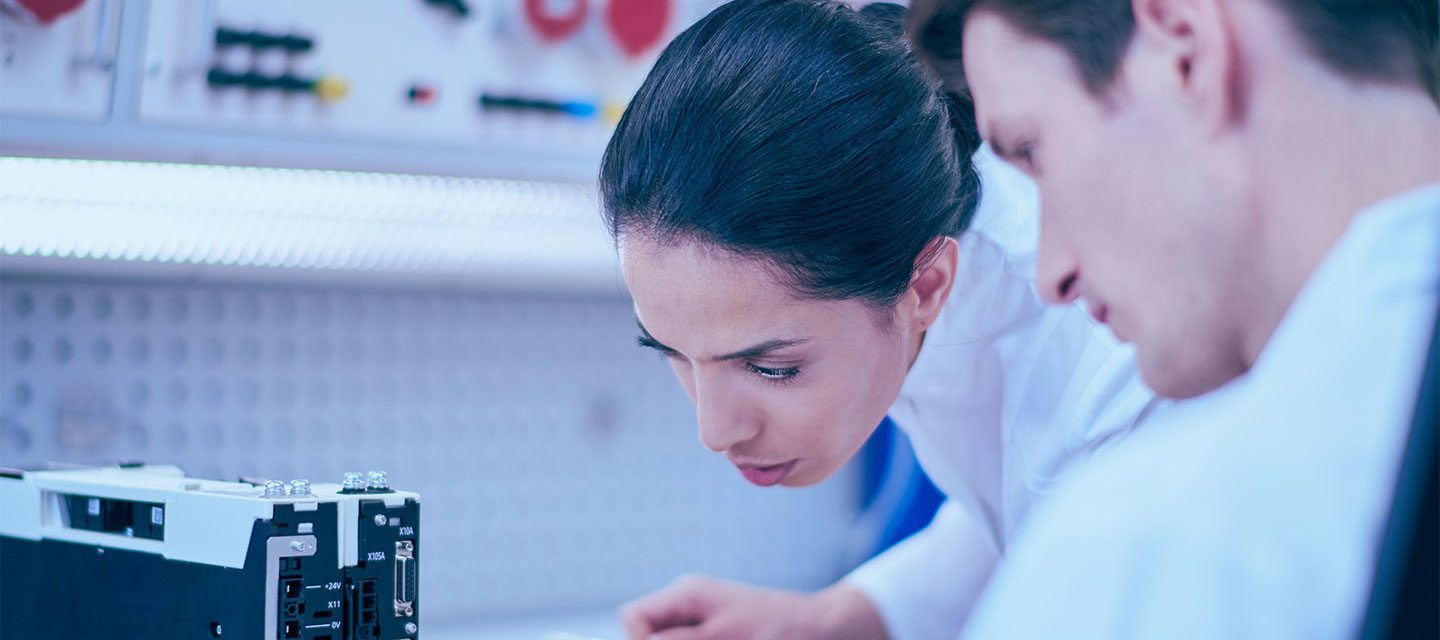
MINAS A6BU servo driver
Real-time control with MINAS A6BU thanks to direct sensor data processing in the servo driver
When it comes to quickly processing sensor measurement data in industrial automation, every millisecond counts.
Highly precise applications for distance monitoring require the servo driver to control the axis as fast as possible. How fast the servo driver responds to the measurement data supplied by sensors depends largely on the cycle time of the PLC used. Valuable time can be lost here because the signal has to travel from the sensor through the PLC to the servo driver.
However, with the MINAS A6BU you can connect the sensors directly to the servo driver. This means you can process the analog data directly in the servo driver without an intermediate PLC. The motor can therefore immediately restore the target distance. The MINAS A6BU uses the EtherCAT protocol for easy integration and cross-manufacturer communication.
Fast, precise, and easy

Your application can also benefit from the direct processing of sensor data:
- No need for an analog input unit
- Simplified system configuration and easier programming
- Reduced signal transmission time
- Higher accuracy
- Smooth control
- Less prone to errors
- Less waste
Mode of operation and system configuration


Possible applications

- Dispenser
Accurate and fast control of the gap between the automatic dispenser and the workpiece - Laser processing machine
Fast correction of autofocus - Lithium battery manufacturing
Precise feeding of bands for highest quality and little waste
Power classes
- 50W to 400W, 1-phase, 100V
- 100W to 1.5kW, 1-/3-phase, 200V
- 2kW to 22kW, 3-phase, 200V
- 600W to 5kW, 3-phase, 400V
Specifications
Encoder feedback | 23-bit (resolution 8388608ppr), 7-wire serial absolute encoder | |
---|---|---|
Control signals | Input points | 10 |
Output points | 6 | |
Analog signals | Input points | 3 (16-bit A/D x 1, 12-bit A/D x 2) Pressure sensor input only via the 16-bit A/D input. |
Output points | 2 (analog monitor 1, analog monitor 2) | |
Pulse signals | Output points | 2 |
Interface | EtherCAT | Real-time communication for command transmission, parameter setting, status monitoring, etc. |
USB | Connection to a computer for parameter setting or status monitoring, etc. | |
Control mode | Position control, velocity control, torque control |