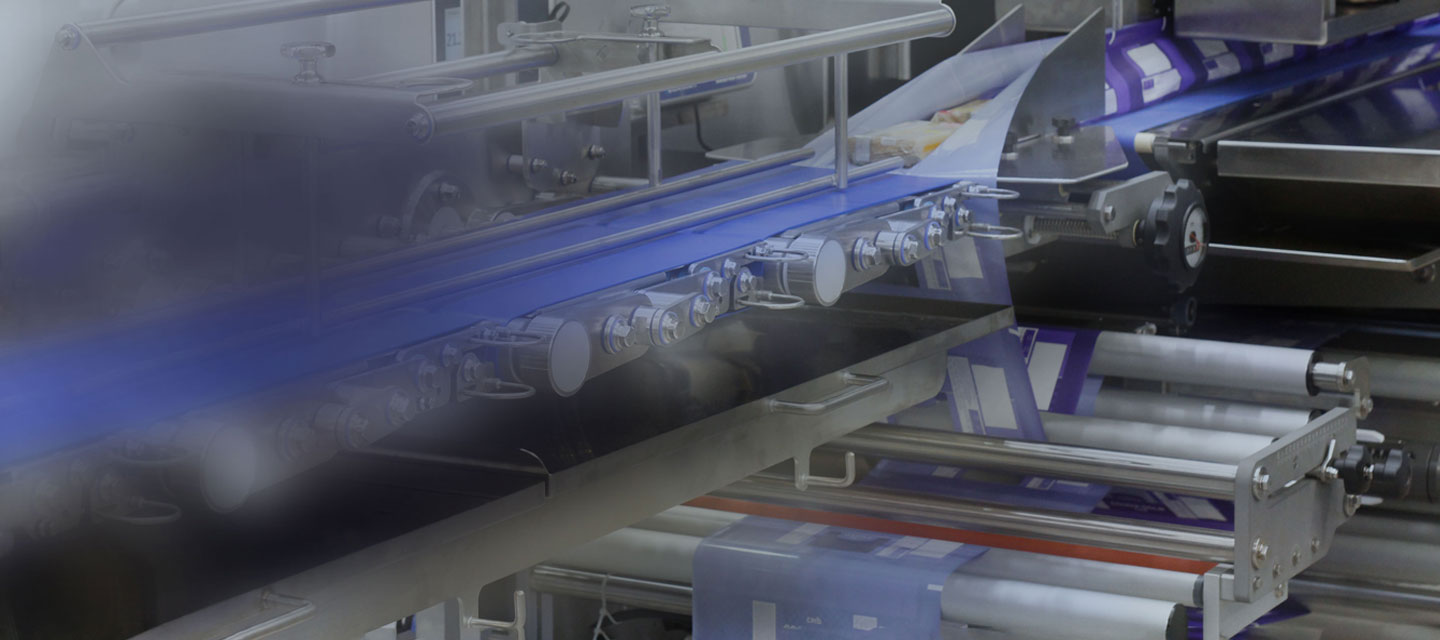
Automation solutions for packaging machines
The packaging industry is always in motion
Ever since the first time a person sent something, packaging had to do multiple things at once – protect new products, adapt to changing aesthetic concepts, and continuously reinvent itself with respect to its material.
In the same way, you, as a packaging machine manufacturer, have to keep up with these trends and continuously adapt your machine concepts to the changing conditions.
The current issues of the industry deal with a plethora of challenges, which can best be described by buzzwords such as sustainability, flexible machine concepts, possible methods to simplify the increasing complexities in mechanical engineering, Industry 4.0 and IIoT.
As broad as these buzzwords and the subsequent issues are, sometimes it’s the minor or seemingly obvious things that can contribute to a situation where a packaging machine operates in a more resource-saving manner, offers your customer a significant added value or simplifies the design for you.
Panasonic provides you with concrete support in your steps to meet the demands of the industry.
Product quality for sustainable machine concepts
We offer high-quality automation products so that your machine can deliver perfect packaging results. However, the Panasonic product quality not only ensures excellent product packaging but also contributes to the sustainability of your machine: The environment benefits from lower usages of resources, e.g. because installed components do not have to be exchanged or people do not have to travel for possible new installations.
For example, our servo drives impress with their top performance and availability and ensure short cycle times and high dynamics in the travel profiles. At the same time, our motors are literally “just install and forget about them”: As a result, your machinery not only scores due to top dependability but also due to its long lifetime. Go online for a first overview of the Panasonic servo drives or use our Product Finder for drives to find out which motor is most suitable for your application.
Mastering complexity – cross-vendor and material independent
Your packaging machine is part of an overall system that consists of stations from different manufacturers. With the open IO-Link, OPC UA and Ethernet communication standards on the field and process level, we provide cross-vendor communication and thereby a smooth integration of your systems in the overall line of your customer. Additionally, our servo drives and programmable controllers are available at EPLAN to simplify the design for you.
Foils and paper – the efforts to achieve more sustainability require packaging machines that can process different materials. Secure significant competitive advantages for your customers with flexible machine concepts: Our broad sensor system portfolio has the right sensors available for this purpose. Use the Product Finder for sensors to compare sensors for your application or contact the Panasonic sensor laboratory: We will be happy to support your individual application.
Other factors that help you overcome your complex challenges are simple programming of the individual components, such as programmable controllers, and a clear visualization on control panels. The Panasonic programming software products enable you to set up our PLCs fast and easily, making them ready for operation in practically no time at all. And, if something does not work as desired, we are right by your side with technical support.
Automation from A to Z
Go online to discover the Panasonic complete portfolio of automation solutions or contact us directly to discuss the challenges you are currently facing with your packaging machine.
Find out which Panasonic automation products can specifically contribute to a perfectly packaged product in the individual machines of the packaging line.
Flow wrapper
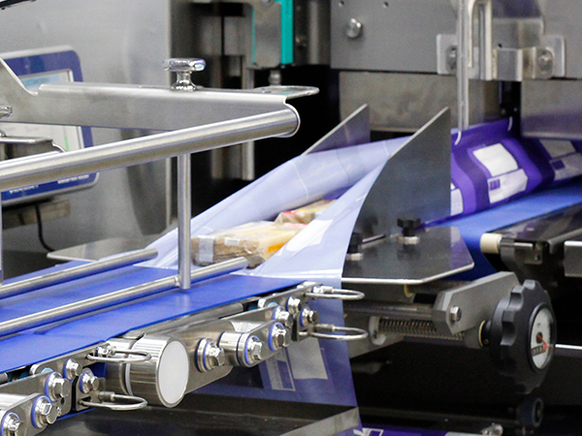
The primary packaging – such as in a horizontal flow wrapper – is the starting point of the packaging line. This first step particularly addresses the perfect packaging of the product in its intended packaging. Machinery at the beginning of the packaging line often work with plastic films. The films must be kept at the correct tension in the feed to be closed and sealed perfectly around the product. For this task, we recommend the compact PLC FP0H, which dependably takes care of the dancer control to control the film tension, but due to its compact size requires little space in the electrical cabinet.
Primary paper packaging can be an environmentally friendly alternative to conventional films. Nevertheless, no sacrifices should be made with respect to design and style in the case of paper packaging. However, especially smooth paper often presents a major challenge for sensor systems. Sensors of the CX400 family detect such packaging dependably and impress with their low energy needs.
Here is a summary of a few additional automation products for flow wrappers:
- The compact PLC FP0H for dancer control with Ethernet ports for cross-vendor communication
- To make sure the packaging films do not become a dust magnet: Ionizer to prevent static charges
- Photoelectric CX400 sensors for paper detection under challenging conditions
- LX sensors for cut mark detection on the packing material
- HG-C laser measuring sensors to inspect the correctly closed packaging by way of triangulation – also available with IO-Link
- Servo drive MINAS A6 Multi to operate multiple axes and with comprehensive safety functions
- Easy machine operation and programming with the HM series touch terminals: from cost-efficient basic models to high-quality touch panels with capacitive glass front, all Ethernet capable for simple integration
- Make your existing machines fit for Industry 4.0 – with the Corvina Cloud, you are providing your customers with a safe VPN solution for remote access to the machine
Laser marking systems
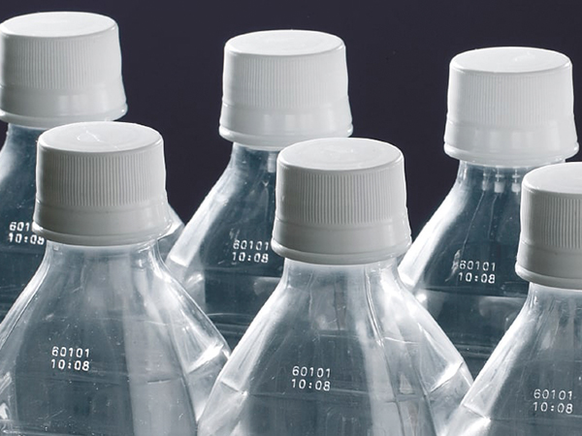
Marking products is an essential part in any production process. The realization of the fastest possible marking is also essential in this process step in the packaging industry. Panasonic laser marking systems allow “on-the-fly” marking at line speeds of up to 240 m/min. For example, this makes it possible to mark PET bottles or film packaging as well as different metals or plastics time-efficiently. In addition to 2D codes or bar codes, it is also possible to mark logos permanently on packaging made of various materials. Panasonic CO2 or fiber laser marking systems can additionally be used to perforate areas for easy opening.
Laser marking systems also contribute to increased sustainability when they are replacing conventional identification systems with paper labels. From an environmental perspective, using laser marking saves labels and carrier film and the laser mark is much more forgery-proof compared to a peel-off label.
Our colleagues are happy to test in our internal laboratory whether or not we can solve your marking task – contact us without obligation or send us the request form with your application data.
Examples of applications of the Panasonic laser marking systems in the area of packaging:
- Permanent marking of different materials
- Secure traceability of products via bar codes or 2D codes
- Perforation for easy opening
Cartoning machine
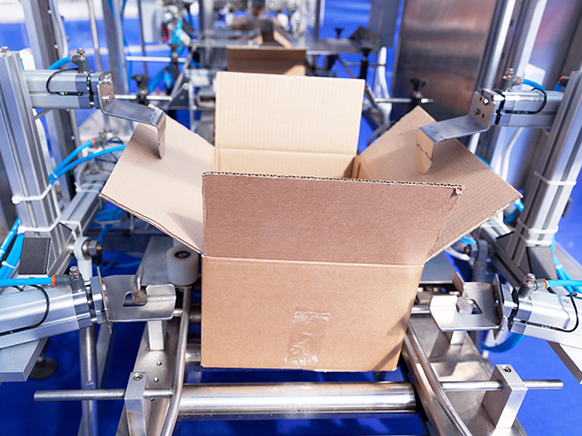
Often, the cartoning machine is the place where individual products are combined in bundles that can easily be transported in cartons or trays. Here, flat cartons are set up, filled with the products and closed or the products are knocked into the carton in the wrap-around process. A major challenge in cartoning machines is the coordination of the various axes with each other: Several infeed axes have to be synchronized with the main conveyor belt to ensure perfect packaging results. The GM1 Motion Controller is recommended for this purpose, as it coordinates up to 32 axes and is easy to set up thanks to its CODESYS programming environment. Another central point when it comes to cartoning machines is the integration of the machine into the customer’s production line. Here, the Panasonic PLC FP7 with its Ethernet connectivity and complete web integration acts as a manufacturer-independent interface.
This is a small selection of Panasonic products that could be of interest specifically for cartoning machines. We look forward to your specific request if you are facing different challenges.
- Motion Controller GM1 for up to 32 axes: Ideal for modular machine concepts
- Reliable detection of the stack height in the carton magazine with our CX400 sensors
- Open manufacturer communication to the command level with the PLC FP7
- MINAS A6 servo drives for dynamic travel
- Reliable glue point detection when closing cartons with the optoelectronic FX sensors – also available with IO-Link
Labeler
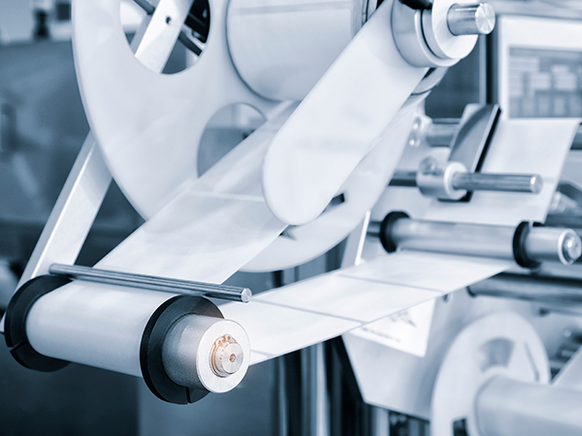
Secondary packaging such as cartons or trays is often marked with a labeling system. In this case, it is particularly important that the labeling process is flawlessly integrated in the overall process of the packaging line. Thanks to open communication protocols, the compact PLC FP0R is seamlessly integrated in the overall system. Additionally, commissioning and operation of the programmable controller is fast and easy thanks to function blocks especially designed for labeling processes. In addition, the marking of secondary packaging must not create a backlog on the conveyor: This means that labelers require highly dynamic drives to implement quick start-up ramps. One of the special features of Panasonic servo drives is their agile acceleration behavior, which makes them an excellent choice for labelers.
Other Panasonic products also support you in inspiring your customers with your labeling machines:
- Reliable detection even of transparent labels or carrier materials with the optical sensors of the CX400, EX10, EX20 and EX30 series
- The compact-sized PLCs FP0H and FP0R require little space for installation and are easily programmable to ensure manufacturer-independent communication thanks to function blocks
- Install and forget: MINAS A6 servo drives for implementing dynamic machine concepts and top availability through Panasonic quality
- Intuitive operation through capacitive glass display with the HMx700 touch panel – OPC UA and Ethernet on board as well as the gateway for the Corvina Cloud, your secure remote access solution
End-of-Line
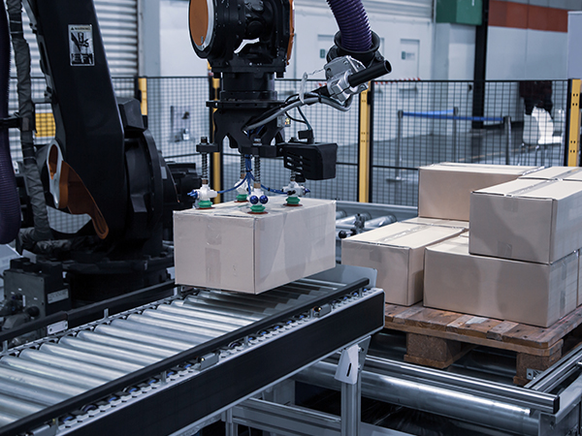
The packaged units can be discharged from the packaging line either manually or automated with a robot gripper. Safety is thereby the top priority, especially when personnel is present directly at the conveyor. Low voltage motors for the operation at 24/48 V DC can be an alternative to ensure comprehensive operator safety. If no personnel is present at the conveyor, we recommend our LIQI servo drives as the most cost-efficient solution.
The use of Panasonic safety light curtains at hazardous points of the packaging line primarily serves to protect personnel. For this purpose, the Panasonic portfolio offers a broad selection of products with finger, hand, or foot protection, which can also be combined without a dead zone to fulfill your individual demands. In addition, at the same time the muting/blanking function can be used to monitor the stacking of the packaging – with IO-Link, your customers can query this data and process it further.
A few products for the end-of-line, with which Panasonic can support you:
- For operator safety directly at the conveyor: Low voltage drives 24/48 V DC
- Broad portfolio of safety light curtains without blind zone, combinable
- Cost-effective conveyor drives with LIQI servo drives
Stretch wrapper
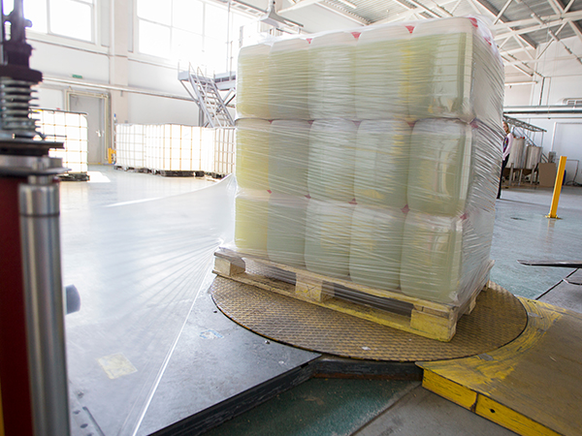
The tertiary packaging protects the packaged products during transport. In addition to heat-shrink processes, stretch wrappers are also used for this purpose, which secure the products on the pallet with film. Whether the stretch wrapper is loaded manually or integrated inline in the packaging line: Users benefit from an aligned automation solution. With servo drives that allow dynamic start-up but can be controlled so precisely that the film roll can be moved very smoothly, Panasonic provides an essential component of this application. The proven sensor system controls the unwinding of the film and the remaining amount of film on the roll to signal a change early on. The Panasonic compact programmable controllers and HMe touch panels also provide you with the perfect tools to offer an effective solution to your customers.
Do you want to make your standalone stretch wrapper fit for the IIoT? Thanks to the FP-I4C Industrial Communicator, existing machines can easily and safely go online: The OPC-UA and MQTT establish the cross-vendor connection to databases and parent systems.
Panasonic is by your side on the way to more sustainability:
This part of the packaging process also causes you to think about more sustainability. Approaches include the minimization of the film thickness to reduce plastic waste or the use of recyclable paper to wrap the pallets. If you are facing the challenge of whether your stretch wrapper will continue to deliver perfect results with these new materials, please feel free to contact us: We can test in our sensor laboratory which of our sensors can reliably detect the packing material in question. Because a new material can also mean different tear properties, it makes sense to check the travel profile of the packaging roll and the rotary table and optimize them for the new material – our colleagues at the Servo Drive Laboratory are standing by to assist you all the way.
Here is a selection of Panasonic products for your stretch wrapper:
- EQ-500 photoelectric sensor reports the end of the pallet height for prompt deceleration
- HMe touch panel: Highly operator-friendly HMI streamlined to the essentials
- No wasted space with the compact PLCs FP0H and FP0R
- Careful handling of thin films: MINAS A6 servo drives
- Ready for industry 4.0: The FP-I4C links standalone machines to databases or the control level
Downloads
Name | Size | Date | Language |
---|---|---|---|
Lösungen für Verpackungsmaschinen | 4 MB | 26.03.2024 | German |
Name | Size | Date | Language |
---|---|---|---|
Bandall user story: Dezelfde drive schept een band | 383 KB | 26.03.2024 | Dutch |
Ranpak User Story: Hoe verpakken bijdraagt aan duurzame ambities? Vraag dat maar aan Ranpak. | 308 KB | 26.03.2024 | Dutch |
Ranpak User Story: How does packaging contribute to sustainability targets? Ranpak has the answers. | 309 KB | 26.03.2024 | English |
Name | Size | Date | Language |
---|---|---|---|
Sensor Selection Guide for Packaging Industry | 15 MB | 12.07.2022 | English |
Name | Size | Date | Language |
---|---|---|---|
Oplossingen voor Verpakkingsmachines | 821 KB | 26.03.2024 | Dutch |
Soluciones para máquina del packaging, envase y embalaje | 842 KB | 26.03.2024 | Spanish |
Solutions for the packaging industry | 4 MB | 26.03.2024 | English |