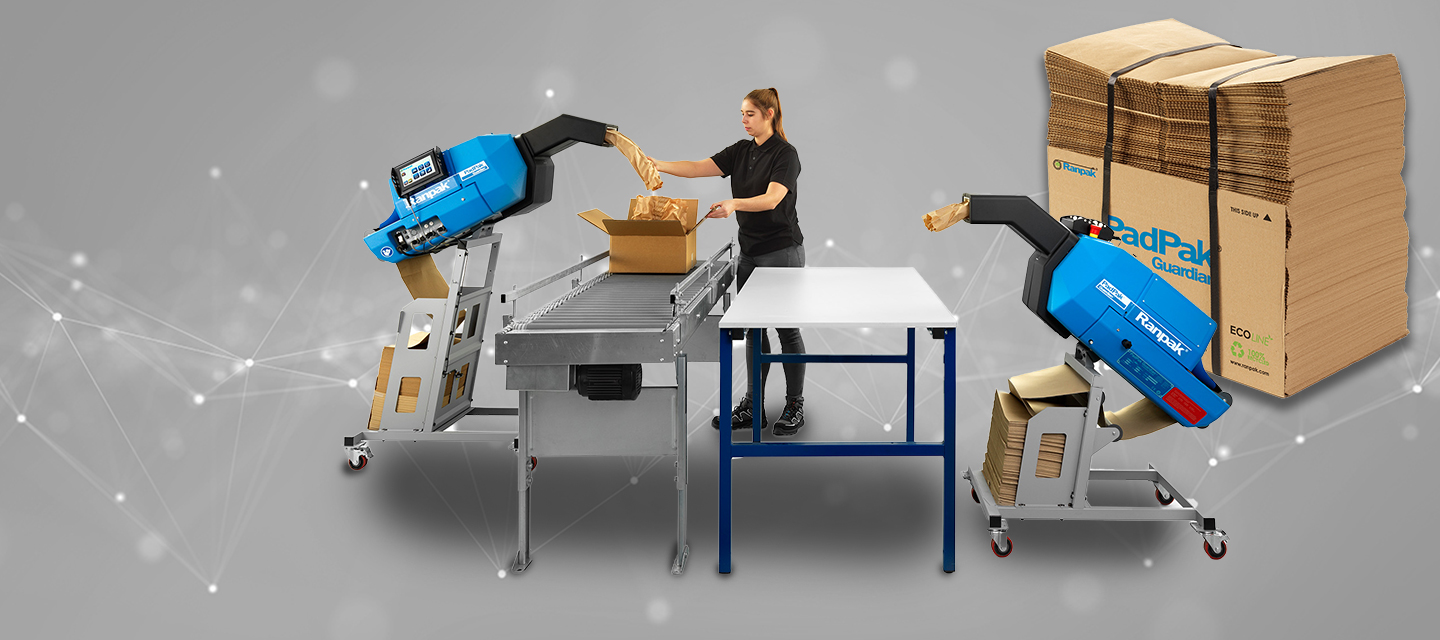
User strory Ranpak: Savings included in every package
How does packaging contribute to sustainability targets? Ranpak, manufacturer and worldwide supplier of packaging solutions, has the answers. The company uses paper to ensure that customers fill their parcels sustainably, quickly and cost-effectively. Impressive sustainability also comes with the PadPak Guardian converter – which features controls developed by Ranpak in close co-operation with Panasonic Industry.
Ranpak produces machines that cut an open box to exactly the right height, to improve sustainability by saving materials and space as well as costs. This trend is further improved by machines that crumple FSC certified paper to fill out the boxes. The paper is a sustainable alternative to plastic that allows the company to contribute to responsible forest management worldwide.
Versatility and automation
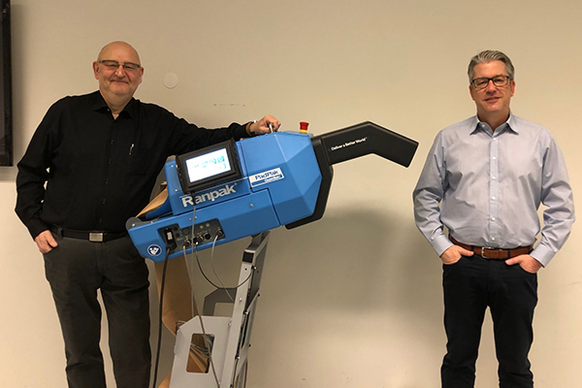
While Ranpak’s sustainable, efficient approach is reflected in their slogan, ‘Build a better world’, their success also depends on two other critical factors – versatility and automation.
The company’s versatility is apparent in how they adapt to each customer’s specific packaging requirements – and Ranpak serves countless industries, from automotive to retail, and from consumer goods to the food and beverage market. Based in Heerlen in the Netherlands, they offer a wide selection of machines that cut paper into any shape.
Engineering manager Rob Pluijmen was reminded of this versatility when he interviewed a candidate for an engineering role. Although the candidate came from the semiconductor industry and was involved with the most advanced technology, he was restricted to working on a single specific part. “He told me how much he looked forward to the diversity offered by a role at Ranpak, and the opportunity to see projects through from start to finish.
“I thought this was an impressive response, and one that reflected the versatility that defines us – not only within our positions, but also in what we do.”
Automation, as the other key success factor, is now fully embraced by Ranpak. Rob comments: “Our machines have sensors, and our engineers can handle all challenges from a small, customer-specific machine adjustment to a fully automated production line. We are also taking steps towards artificial intelligence, intended for predictive maintenance, for example. But also think of a machine that determines what type of cardboard is being used, what the thickness is, and then automatically adjusts the settings accordingly.”
Compact converter
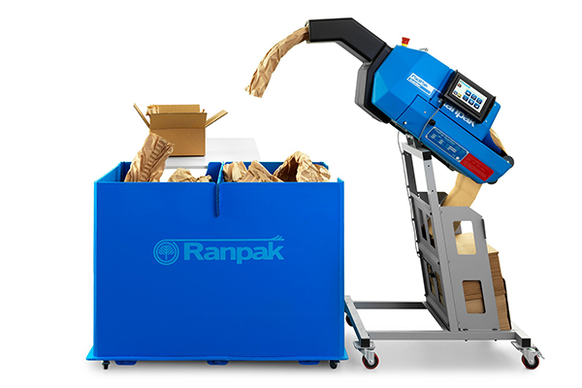
The PadPak Guardian is an excellent example of how Ranpak is improving their paper packaging technology while applying more advanced automation. This new generation converter, which converts paper into buffer material, is compact and relatively lightweight, and therefore easy to move. That makes it flexible in use, says Ad Veldt, senior electrical engineer at Ranpak who is closely involved in the Guardian’s development. “The table model version is also new, and customers can use it in many ways.”
Size had proved to be a stumbling block for the Guardian’s predecessors, according to Ad. “The earlier machines were bigger, which was not always useful in warehouses. We accommodated our customers’ feedback within our new machine, while also choosing a modular design. Modules are easier to ship and can also be replaced much faster.”
Towards a uniform platform
In addition to its lighter, smaller form factor and modular design, the Guardian features new, improved controls to replace the outdated system on its predecessors. In doing so, the machine becomes the first implementation of a uniform platform that can be applied to Ranpak’s entire product family.
To develop these controls, Ranpak worked closely with Panasonic Industry’s applications engineering team based in their Best, Netherlands facility. Ad comments: “This development went very well; partly thanks to this collaboration, we completed this project in about three months. I made good progress myself with the software, partly because it was set up so clearly by Panasonic. And if I encountered problems, I quickly received the right support.”
The whole control package
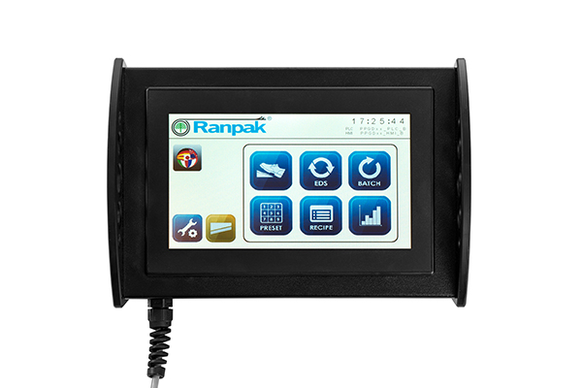
Panasonic Industry provided the converter with a user-friendly human machine interface (HMI), presented on a magnetic, easily movable screen. They also delivered the custom printed circuit board, while their team wrote the control software and built the control unit housing.
“This was an almost complete control package,” says Roel Lommers, key account manager at Panasonic Industry. “It also made the project special for us. Everything came together, and all within Ranpak’s tight completion deadline. It seemed ambitious, but we managed it between us.”
The Guardian project was the first collaboration between Ranpak in Heerlen and Panasonic in Best. Ad comments: “We were new acquaintances, but it soon became apparent that everything was properly coordinated. Becoming effective quickly depended on generating clear documentation.”
Rob also looks back on the collaboration with satisfaction. “No question was ever too much. Moreover, in addition to their extensive product selection, Panasonic always gave us solid advice – and their skilled team in Best delivered our versatile set of controls as well.”
Ranpak: Rapid growth and significant transition
Ranpak’s packaging solutions service to customers worldwide is growing and evolving. This is evident in Heerlen, where engineering manager Rob Pluijmen notices how fast the company is developing. “We have grown tremendously and are continuing to do so. The climate debate certainly plays a role in this; companies want to move towards sustainable alternatives. Now that the coronavirus crisis is also creating so many online orders and therefore packaging, this growth has further accelerated.”
Ranpak is transitioning as it is growing. Rob explains: “We are increasingly a solution provider rather than just a product supplier. From the moment a box is put on the conveyor, to the point that it is loaded into the truck: we play an increasingly important role in the entire process.”