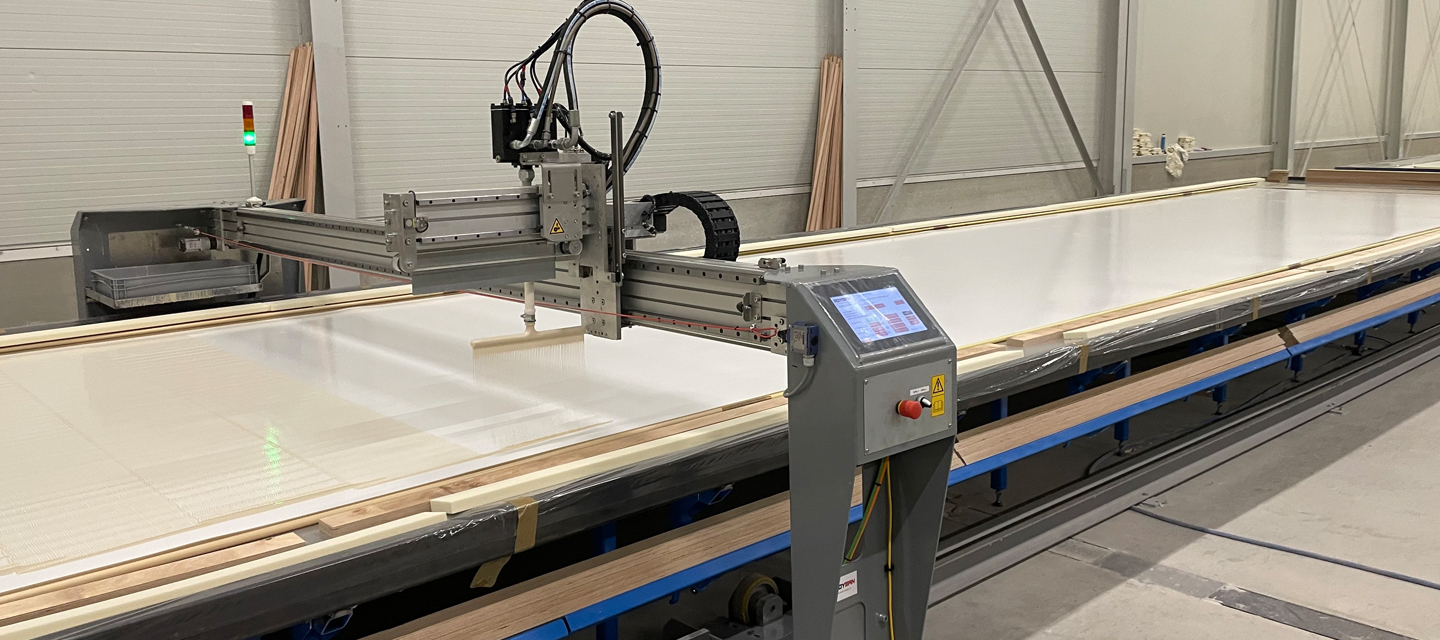
With smart automation, job satisfaction grows
Royman EA is still young, but as a technical partner for the manufacturing industry and production companies, it is making significant strides. From its own workshop in 's-Hertogenbosch, its portfolio is filled with special projects, including those for special machine construction. Take, for example, the gluing machine. Powered and controlled via a solution from Panasonic Industry, it takes on a lot of work for the producer Albuco. This results in flexible production and, even more importantly, less work pressure for the staff.
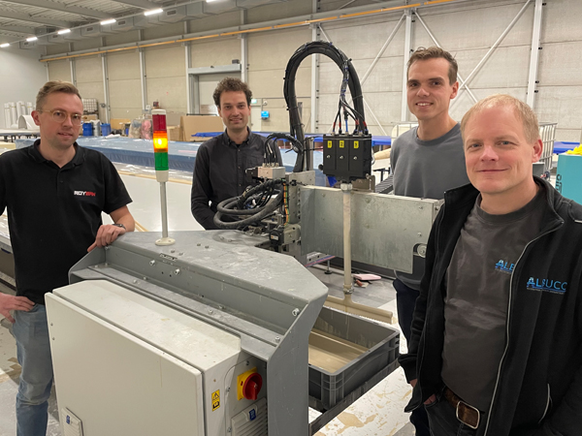
They are happy to contribute to larger projects, for example, with other machine builders. But the most beautiful part? For Leo Hartman and Patrick Roijers, it's their own projects. That's where everything comes together, and as technicians, they find their passion. They met during their higher technical school studies in Engineering, Design & Innovation, and in 2020, they started their company, Royman EA. It is based in 's-Hertogenbosch, Brabant, where they still work together in the workshop. Yet, they can handle their special projects well together, Leo emphasizes. "Patrick and I do everything ourselves; we both have a vocational education background. He started as a metalworker, and I was an automotive technician. This combination of vocational and higher education works very well. We design a structure, but we can also weld it, for example. This way, we can proceed directly."
Automating repetition
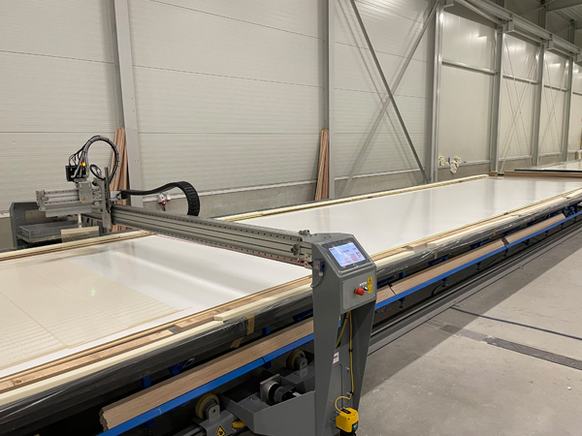
The outcome of such a comprehensive project is evident here in Dinxperlo, just a stone's throw from the German border. This is the location of Albuco, which manufactures insulation panels for vehicle construction. It's a specific process where applying glue between the different components is partly done manually. It's a labor-intensive task, although Marco Halfman, the owner of Albuco, doesn't want to completely eliminate the manual work.
"We also produce custom work here. That requires craftsmanship and careful inspection by multiple employees. But for standard production, we wanted to move towards further mechanization. Constantly performing the same repetitive motion causes significant strain, both physically and mentally. That's why it was time to make that strain manageable. Variety in work is important; I want people to be able to do their jobs as pleasantly as possible here."
Equal amounts of glue everywhere
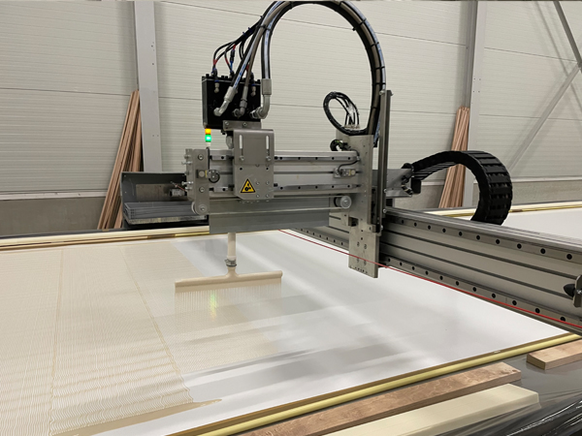
Marco found Royman through connections and asked Leo and Patrick for a solution to automate the gluing process. The two engineers designed and developed the solution. They then built, installed, and tested the gluing machine, which moves over two tables, each sixteen meters long, in the hall. While the frame slides over the rails
on the ground, the glue spreader from the dispensing machine evenly distributes the glue over the panels.
The process appears streamlined, and according to Patrick, the machine was built relatively smoothly. "The challenge was mainly in optimizing the movement. It needs to remain consistent, even when the glue spreader moves in the opposite direction at the end of a row. Nevertheless, we also managed well with the mechatronics and control, thanks to the help from Panasonic."
The right feeling from the start
Leo clearly remembers striking up a conversation with Roel Lommers, business development manager at Panasonic Industry, during a trade fair. "Royman is a small company, and you might think that wouldn't make us very interesting to a large corporation. But during that conversation, there was a lot of interest in us. I was looking for a servo package for the machine at Albuco, and Roel and his colleague gave me extensive advice on it right there at the fair."
Leo says the good feeling was there quickly. "That's why we chose Panasonic, which later supported me in working with the CODESYS platform. They also assisted during the installation via TeamViewer, and importantly, we received all the components within the specified time."
A young company on the move
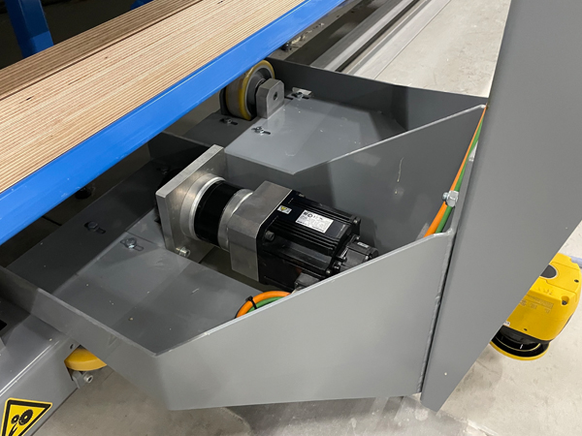
The gluing machine at Albuco includes motors and drivers from Panasonic Industry, which also supplied the gearbox, motion controller, and HMI panel for the installation (see box 'Extra Driven, More Flexible'). Together, all these components provide a specific total solution, Roel explains. "What are the conditions for a good distribution of the glue? What are the drying times, and at what temperatures does that occur? Royman mapped all of this out for us, allowing us to tailor our advice accordingly." Roel finds it simply enjoyable to help a young company get on its way. "The vast majority of this solution is Royman's own work. But where possible, we contributed our thoughts; we are more than just a supplier."
Now that the gluing machine is operational, Royman is awaiting the next project at Albuco. This project focuses on cutting polyester material, which still requires precise and intensive manual work from Albuco's staff. It is up to Royman to have this task taken over by a new cutting machine, which will also be powered by products from Panasonic Industry. Soon, there will be two machines in Dinxperlo that, according to Patrick, demonstrate what Royman is capable of. "Someone has to give you the opportunity, as Albuco does. This takes us further, and it's great that Panasonic is also supporting us with this project."
Extra driven, more flexible
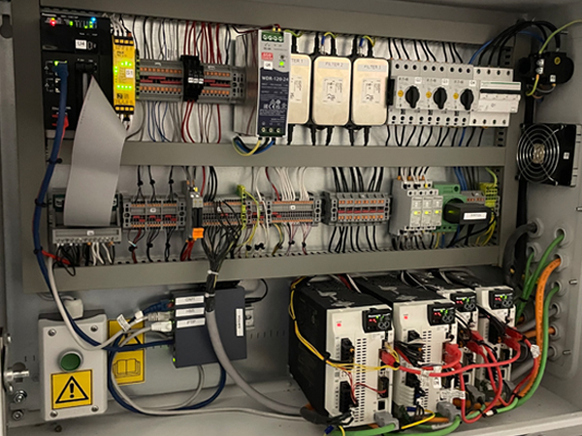
For the gluing machine, Royman EA worked closely with Marco Halfman, the owner of Albuco. "We quickly got into the details together," says Leo Hartman, co-owner of Royman. "Marco, like us, has a technical background. We speak the same language, which works very well." It was a considered choice to initially have the machine move via a motor on one side. "However, we noticed that it wasn't stable everywhere," says Leo's partner, Patrick Roijers. "The arm of the machine wobbled a bit, which we fixed with an additional motor along the rail on the other side."
Both servo drives are from Panasonic Industry's MINAS A6 series. In the control cabinet, there are four MINAS A6 servo drives lined up at the bottom right, with Panasonic's GM1 motion controller in the top left corner. This controller connects to the servo control via EtherCAT. It also has an Ethernet connection to the HMI screen provided by Panasonic, allowing an operator to easily retrieve data from an external database via an FTP server. A versatile total solution, much to Marco's satisfaction. "It takes away a lot of difficult work, and we can manage with fewer man-hours. On days with fewer staff, this machine keeps our production flexible."