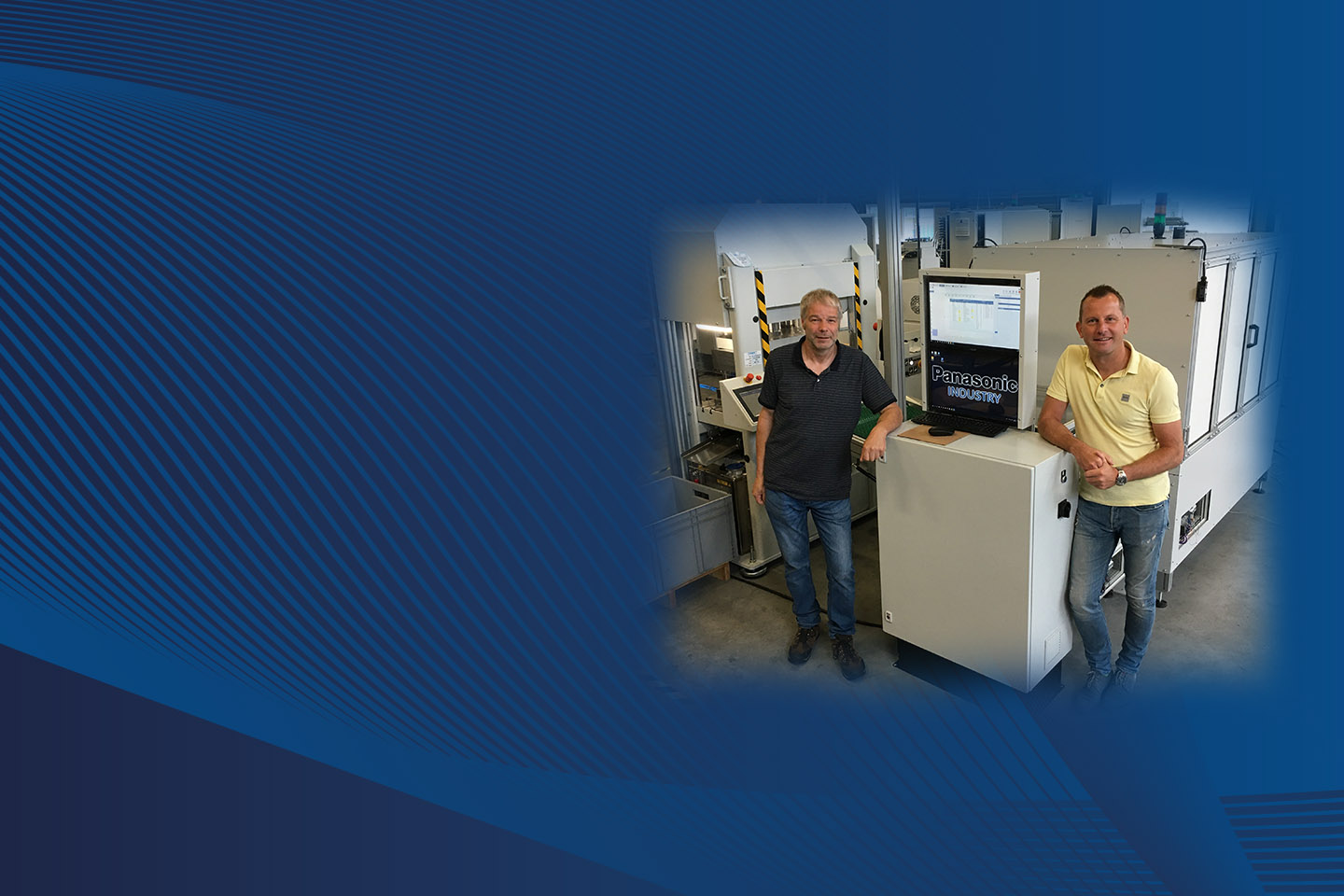
User story Crest Dutch Machinery
Customer demands change. They know this at Crest Dutch Machinery in Raalte, which makes production lines for number plates in addition to numerous lamination solutions. Each line order has its own characteristics, and the need for data logging is always increasing. It's up to Crest to respond and they work together with Panasonic Industry, which has already equipped many lines with a laser coding and vision system.
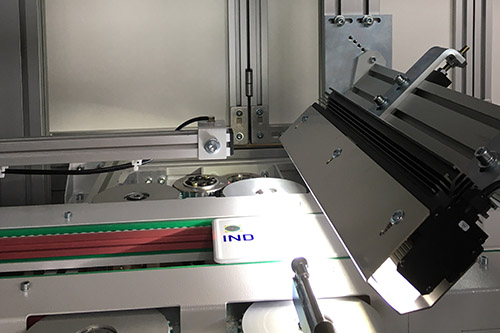
Having the necessary techniques in-house makes it quick to change gear and quickly respond to what is needed at that moment. Take, for instance, the unwinding of basic material for mouth caps: at Crest Dutch Machinery in Raalte they made a machine for this last year. The basis was already largely in place, the customisation was in the last ten, at most twenty per cent. This created space to add their own knowledge precisely there, as Jos Reimert likes to do.
"Where does a customer want to go; how can he be helped in the best possible way? With a modular approach, we can answer those questions even better."
Jos is Technical Director at Crest, which is considered a specialist in laminating solutions. The company makes machines that provide sheet metal and flexible materials with films and self-adhesive layers. Crest also produces machines to cut these materials. In terms of application, the link with signing comes up first, Jos realises, although that market is now only a small part of the customer base. "Most of our machines are for industrial applications. Think of laminating touchscreens, laminating applications in cleanrooms and insulation materials for the automotive industry. Competition is certainly there, but we have always been strong in specials. Customers know that; they often come to us 'via via'."
Advanced bundled
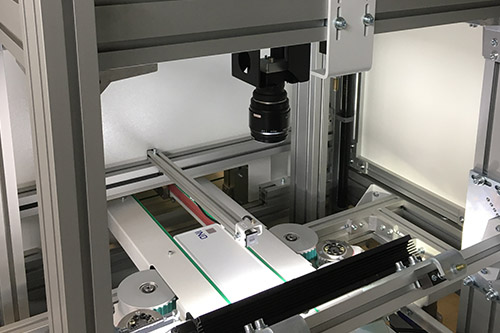
The latter also applies to complete lines for the production of number plates. Crest develops and produces several such installations every year, and after extensive testing and checking, supplies them to customers around the world. According to Jos, feel free to call it a niche market, with only a few manufacturers worldwide. "Many countries have only one licence plate line, moreover, such a production line is quite sophisticated."
When realising a license plate line, Crest is at the forefront of the process so that Jos and his colleagues can think along and adjust sufficiently, thus equipping the machines with the necessary technology. That it is suitable for remote use goes without saying, according to Jos. "Should the situation call for it, we can watch remotely online and read data with it."
Need for control
Speaking of data, by far the majority of current developments are in that area, Jos explains. "Customers now want to be able to safeguard the entire production process. To log everything and turn it out on paper can only be done by controlling the process externally and centrally." Jos picks up a number plate and points to the top of it. "On this will be a serial number, on the back follows a barcode with yet another number linked to it. These are basically two separate systems, although they do have to run parallel to each other. The numbering must not pass each other, which can only be done by sending external data to both systems."
It is up to Crest to respond to the need for such central control along with a partner like Panasonic Industry, which has been co-supplying its production lines with vision and laser coding systems since 2006. Jos remembers how the partnership came about back then. "The immediate reason was the laser head: it is quite small, which once in the line provides space and convenience. Anyway, that was then. Now the strength of the cooperation 'lies mainly in the support and thinking along with our customer requests."
Strengthening over and over again
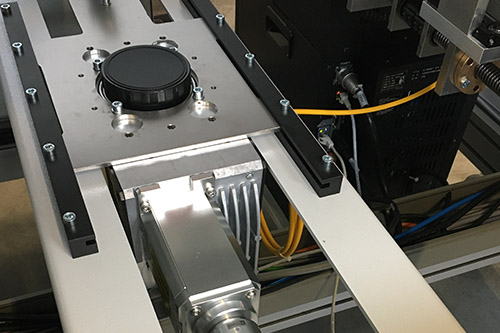
While Crest assumed control via industrial Ethernet with the previous generation of licence plate lines, PROFINET is now the standard. "So, we apply our latest type of lasers for Crest," says Ronald van Seters, key account manager at Panasonic Industry. More specifically, these are lasers from the LP-RF series, which enables control via PROFINET. Another feature of the lasers is the demountable head, which offers security during transport. Ronald: "The fact that the laser head can be disassembled came from discussions with customers such as Crest. There appeared to be a need for it, after which we incorporated that demand into our product. We strengthen our customers, but the reverse is equally true."
A collaboration that broadens, driven by changing end-customer demand. In any case, there is no question of just delivering, Jos argues. "What is the scope, what does the customer want? How are we doing now, what do we have to change to make the new line also perform optimally? All these questions come up in our discussions with Panasonic. The cameras in the vision systems have become more compact, the lasers even more advanced. But what ultimately matters is knowing which product to apply when and Panasonic helps us do that."
Moreover, Ronald notes, it's not even so much about the technology as such. "Especially in these times, with for instance less interaction due to working from home, it is so important to keep people engaged. We bet on that at Panasonic, and I notice that Jos does the same here at Crest. It's nice working together. You can have all the knowledge you want, but in the end it's all in people. So that they can do their work as well as possible: ultimately, that is the goal."
Every material has its impact
Crest Dutch Machinery has forty years of experience in laminating solutions and has over twenty permanent employees. Development, engineering and production all take place in Raalte in Overijssel, after which Crest's machines go to customers all over the world. It is a specific market, which calls for specific knowledge of both the technology and the materials to be laminated, explains technical director Jos Reimert. "Each material has its own characteristics, which together impacts many parameters. Roller pressure, temperature and speeds: we have to take a lot into account. Tolerances are very small, which requires a precise look."