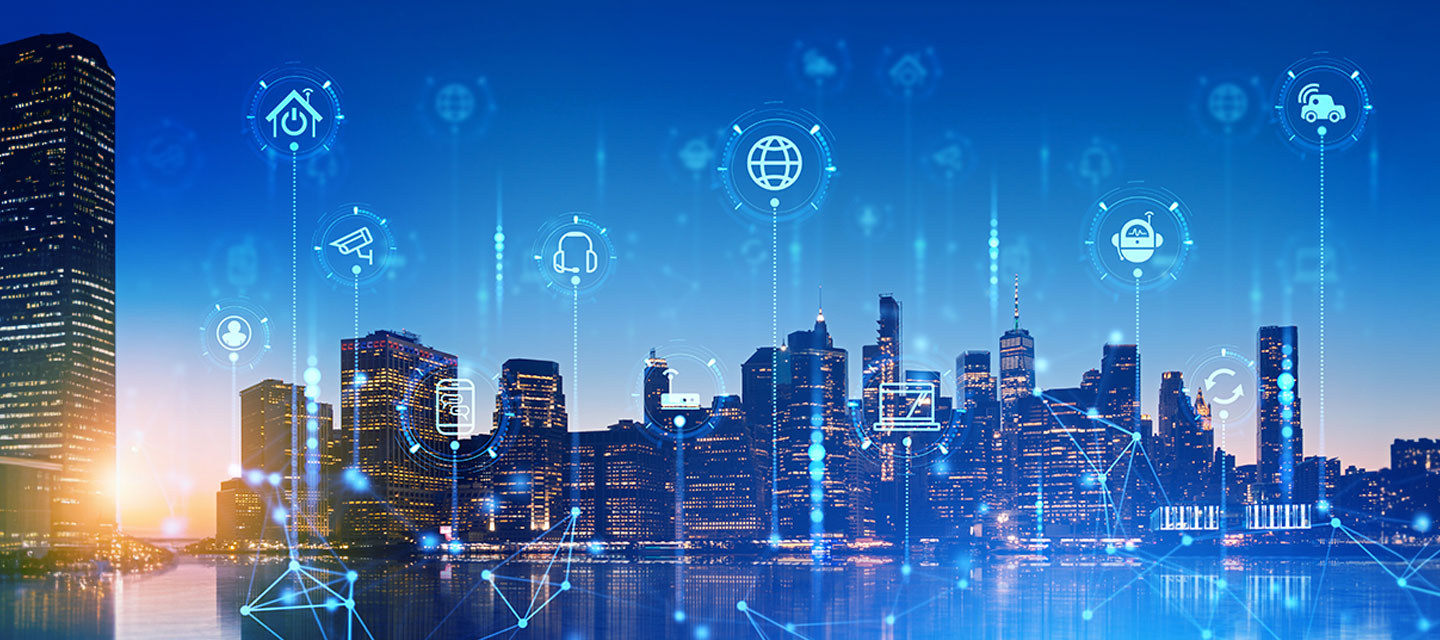
Remote diagnostics: connecting expertise with global operations
Many maintenance operations are repetitive and don't require physical presence. Why not simply perform maintenance from your office? This saves time, labor costs and travel expenses, while allowing one operator to monitor multiple machines simultaneously. Discover the power of remote diagnostics, as your window into global operations.
Maintenance from anywhere, anytime
Remote diagnostics fundamentally changes how you maintain equipment by breaking down geographical barriers. Through secure network connections, your technical teams gain instant access to machine data, error codes and performance metrics – all from a central location. Ready to reduce maintenance costs and improve response times? Here's how to build a robust remote diagnostics framework.
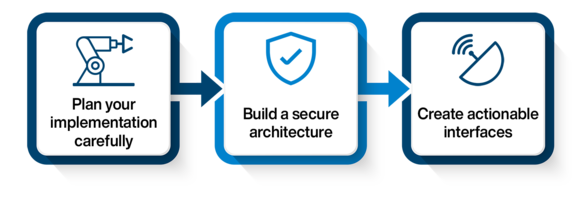
Plan your implementation carefully
Start by identifying critical machines requiring monitoring. Assess your existing network infrastructure for suitability, including available ethernet ports and IP ranges within your factory environment. Thorough preparation forms the foundation for successful implementation.
Build a secure architecture
Protect your critical assets with up-to-date security standards (SSL/TLS, SSH, HTTPS) and gateway protection. Configure firewalls with appropriate IP restrictions within your IT/OT networks and establish a VPN server for secure machine connections. A system with detailed audit trails and role-based access control ensures only authorized personnel can connect.
Create actionable interfaces
Deploy visualization solutions enabling remote connectivity, either through webservers on PLCs or dedicated HMIs within your OT network. Develop an integrated error handling system with standardized error codes, timestamps, troubleshooting suggestions and an error buffer for historical data. This transforms raw diagnostic information into actionable insights.
Leverage the power of virtual presence
Don't let distance limit your maintenance capabilities. With a solid foundation, implement an effective remote diagnostic workflow: