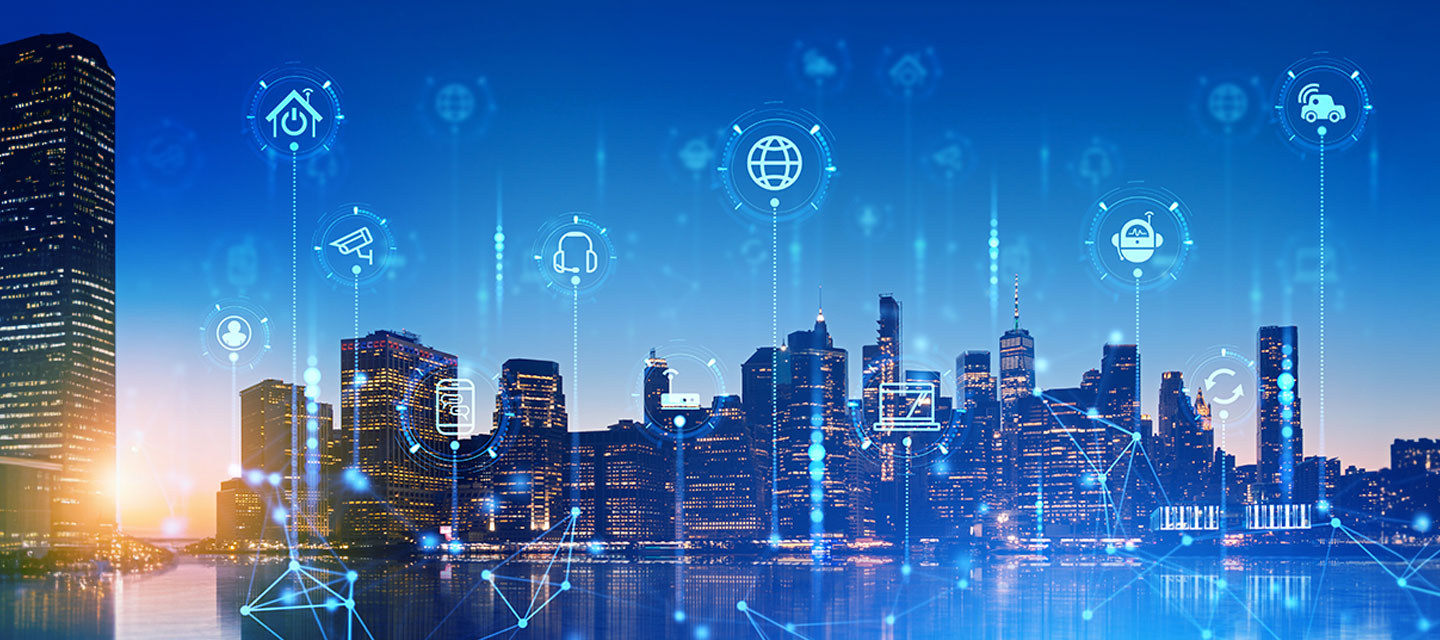
Process optimization: turning machine data into manufacturing excellence
Did you know that the average manufacturing facility operates at just 60-70% of its full capacity? Inefficiencies, unplanned downtime and quality issues drain your resources daily. Imagine having complete visibility into every aspect of your operations, pinpointing exactly where improvements are needed. It’s time to take control with overall equipment effectiveness (OEE).
The 4 D's: your path to process excellence
Process optimization focuses on improving manufacturing efficiency while reducing waste. OEE has become the standard that helps you enhance availability, performance, and quality. Ready to take these components to the next level? By following four essential D's – define, design, deploy, and develop – you maximize the impact of your manufacturing processes.
1. Define your objectives
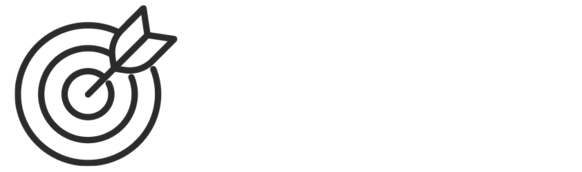
What are you truly aiming to achieve with your OEE implementation? Begin by identifying specific goals such as reducing downtime, boosting productivity, or enhancing quality. The equipment you select should have the greatest impact on your operations. A clear definition of how measure availability, performance and quality provides the framework for all future optimization efforts. Start by assessing your current performance to establish a baseline for comparison.
2. Design your data pipeline
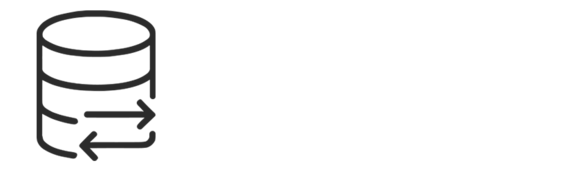
Effective OEE implementation starts with the right data architecture. Select appropriate sensors and acquisition devices to monitor your machines. Identify critical data points that influence availability, performance, and quality with valid timestamps. Configure PLCs to process sensor data and include variables defining machine status. Plan how to integrate your OEE system with existing ERP and MES platforms for a complete solution.
3. Deploy with precision
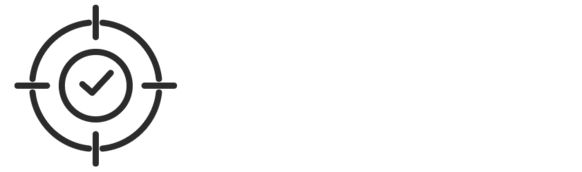
Real-world conditions often reveal unexpected challenges. That's why your OEE system should be tested thoroughly before full rollout. Only then can you ensure data accuracy and system reliability. Validate your metrics in different scenarios; do they align with manual measurements? If so, your system is ready. And don't forget your people: trained operators make the difference between raw data and real-time action. Rolling out the system properly across your selected machines or production lines is crucial for success.
4. Develop continuous improvement
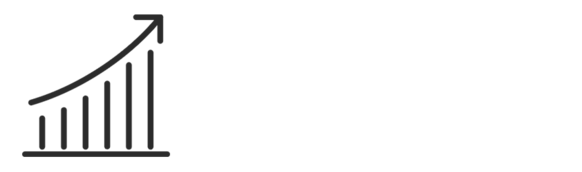
The real power of OEE emerges when data transforms into actionable insights. Establish a continuous monitoring process to identify trends, bottlenecks and improvement opportunities. Create feedback loops that incorporate these insights into your initiatives. Use your OEE data to drive enhancements in equipment performance, maintenance schedules and production processes. Companies that master this approach consistently achieve world-class OEE levels.