Servo solutions for semicon: provide your machines with the right balance
The miniaturisation of chips continues. They need to be increasingly smaller, while rising market demand increases the pressure to produce faster. This creates a tricky balance and calls for high-end servo drives, for an optimal balance between precision and speed.
MINAS A6, for your process
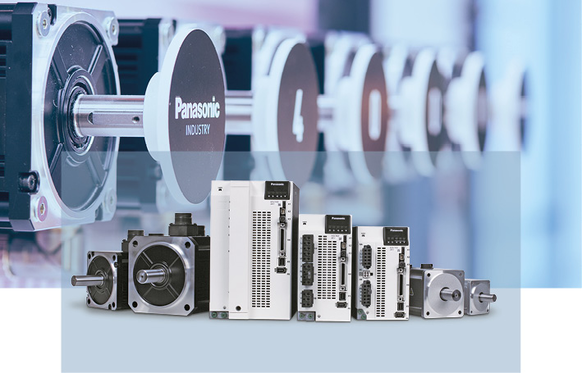
Experience the functionality of our MINAS A6 servomotors. Although 30% smaller and 20% lighter than their predecessors, they offer everything for your process. Think, for example, of an EtherCAT interface, to a high-resolution 23-bit encoder and to motors ranging in power from 50W to 5kW. Moreover, the A6-Multi versions have 18 integrated safety functions which comply with SIL/PLe safety regulations.
Keep control everywhere
Improve wafer positioning, make the movements of handling robots as smooth as they are precise. With A6 motors, you ensure control at every level. And its integration? With our customisation, we make your application customer-specific. We are close by from our local offices, and also offer the benefits of an international parent company.
More precise, faster and robust. On every level.
In a market as dynamic as semicon, staying behind is not an option. Therefore, take the functionality of your machines and equipment to an even higher level. With our MINAS A6 servomotors, you give new substance to a precise and reliable semicon process.
Precision for dicing
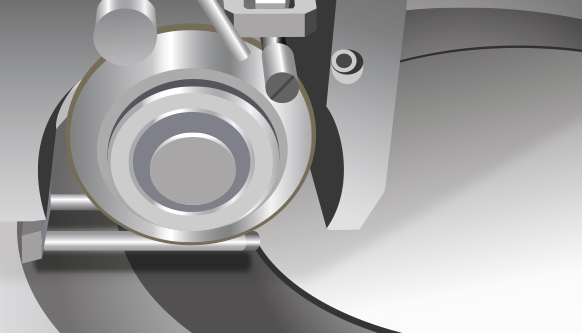
Wafers only a few micrometres thick, and then cutting chips from them. This requires extremely precise positioning and movement. Our A6 servo system ensures the highest degree of precision. So, how minuscule does it have to be for you guys?
Chip picking without vibrating
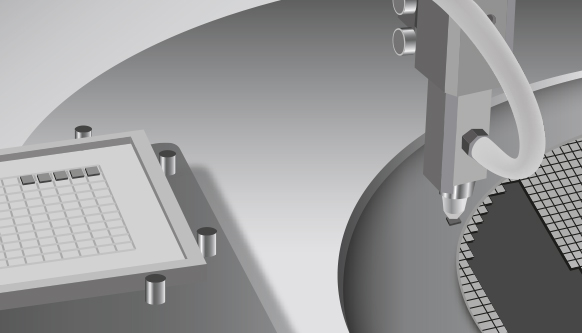
Faster than fast. But with the highest degree of precision. The A6 servomotors combine both for chip moving. The drives distinguish themselves with a high frequency response, which prevents vibration through the chip transfer machine.
Efficient spin coating
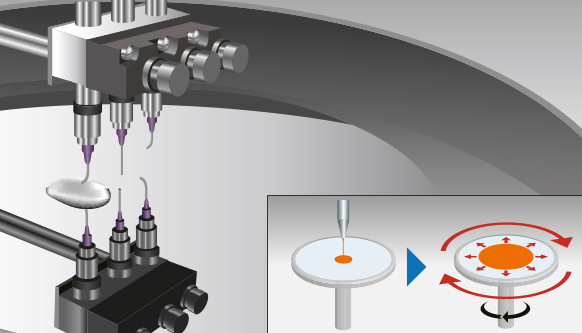
Our servo motors achieve high rotation speeds. And thus give a spin coater a high centrifugal force. While that provides the wafer with an extremely uniform layer each time, excess solution is effectively removed. This is efficiency for the semicon process. Spin after spin.
Let’s talk about it! Contact our local specialists. We would be happy to tell you more!