Panasonic Industry's ETQP series of power inductors - the choice for most demanding automotive applications
When Panasonic started the development of the first metal composite power inductor nearly two decades ago, the key target was to design a product that would be able to withstand severe conditions and provide the highest reliability for automotive applications.
Nowadays, Automotive engineering witnesses almost dizzying progress in electrification. Correspondingly, the demand for passive components such as coils reliably withstanding harsh automotive conditions is higher than ever before. And it’s not only about constructive toughness and heat resistance: At the same time, there is a clear trend towards ever smaller components to save space and reduce weight.
With the introduction of the ETQP-series, those requirements were not only met, but in many cases even exceeded. In the following, we will briefly spotlight those key design elements that substantiated the PCC’s excellent reputation in many fields of applications:
Monolithic structure
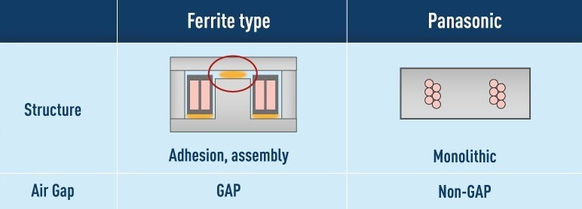
Back then, when the development of the first metal composite inductors started, power inductors were basically all made of ferrite. This type of inductor consists of several sintered parts which are combined and come with an air gap inside the body. Due to its assembled structure, the resistance to vibrations of ferrite inductors is limited from <4G to a maximum of 10G.
In contrast, the Panasonic Industry metal composite power inductor has a monolithic design by pressed metal powder around the copper wire. The monolithic structure leads to a much higher vibration resistance, up to 30G - depending on the series.
Terminal structure
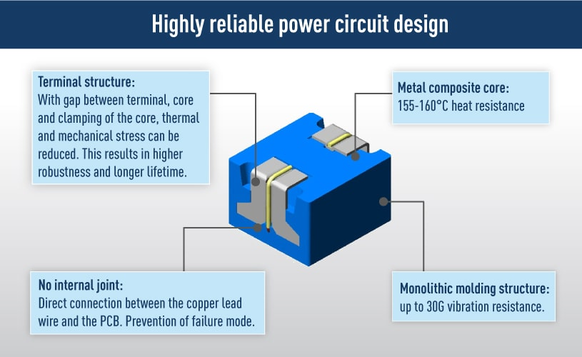
Another important feature that guarantees the highest reliability is the terminal design. The gap structure between the backside of the terminal and the core minimizes solder joint crack issues caused by thermal stress. Furthermore, a unique terminal structure without an internal joint ensures superior vibration resistance. The ETQP_M___Y__ - series leads the copper wire from the inside core to the bottom of the outer terminal, enabling a direct connection to the PCB and safeguarding the highest mechanical joint solder connection stability.
Temperature resistance
As temperature requirements are getting more and more demanding in automotive and other customer applications - not least because the component density in modern vehicles is increasing more and more - it is crucial that a power inductor can withstand high temperatures over a long lifespan. Depending on the type, the ETQP series is specified for operation up to 160 °C including self-heating. This is possible because no adhesives are used in the design, which is typically a weak spot for temperature resistance. The resin material of the core itself as well as the coating of the copper wire have a heat resistance of over 200°C.
High vibration resistant type
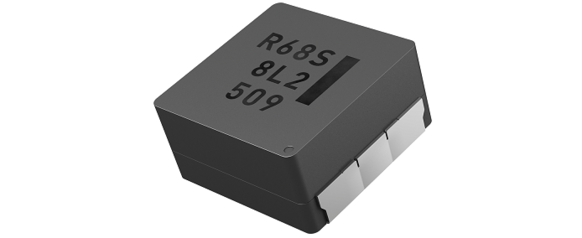
Although the standard ETQP types already offer a very high vibration resistance, there are some applications that require an even higher specification, for example, PCBs which are mounted directly on a motor or powertrain. Panasonic Industry tackled this challenge and developed the ETQP_M___YS_ series, ensuring resistance to vibrations of up to 50G. This has been made possible by lowering the centre of gravity with a change in the terminal structure – so this series is ready to use in even the most demanding environments.
Summary
In summary, with the ETQP-series, Panasonic Industry created a power inductor whose monolithic structure of the metal composite core in combination with the terminal design and thermal robustness leads to a product with the highest reliability for even the most demanding automotive, high temperature, high vibration applications, throughout the lifespan of a modern vehicle.