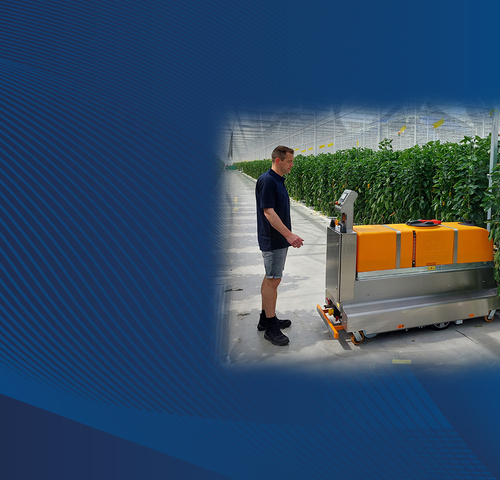
User story Berg Hortimotive
Differentiate yourself with just one product? No company can survive on that anymore. Open communication, knowledge sharing and using people’s strengths is what makes the difference. Take, for instance, the project that Panasonic Industry undertook with Berg Hortimotive, which specialises in logistics solutions for greenhouse horticulture. Challenges in the supply chain called for an urgent change. This turned a long-standing customer-supplier relationship into a close collaboration in many areas.
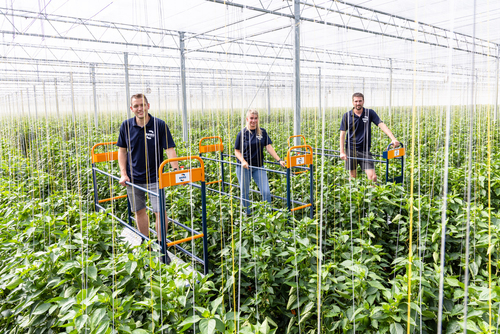
Berg Hortimotive has been active for more than fifty years in the world of greenhouse horticulture, pioneering and leading the way. Based in De Lier in the Westland region of South Holland, the company works on logistics solutions that speed up and improve greenhouse processes, making them much more efficient. Take the tube-rail trolley, for example, which allows growers to quickly care for crops at height. Tens of thousands of these trolleys are now on the road to customers worldwide and although other manufacturers now offer similar solutions, the very first tube-rail trolley was developed here. Frank Bos, supply chain manager at Berg Hortimotive, believes that such a groundbreaking invention should be celebrated; "We are somewhat modest, which suits us. But still, a bit more pride is allowed."
When supplies suddenly stall
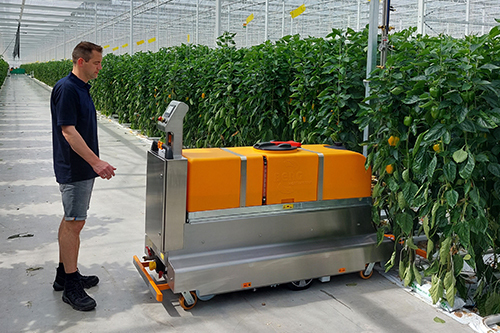
With the growing, global demand for food, greenhouse horticulture is changing in abundance. So, Berg Hortimotive is responding broadly, with logistics solutions for crop care, harvesting & transport and barn automation, among others. With HortiKey's data-driven systems, the company answers the demand for the most accurate harvest prognosis possible (see box 'The harvest moment predicted'). Finally, what about crop protection? For this Berg Hortimotive has the (fully) automatic BeMatic Meto spray robots.
Equipped with spraying equipment and travelling on a rail system, the Metos save horticultural entrepreneurs a lot of time via a sophisticated interplay of several control components. For years, their deliveries - then via another party - were no problem. Until the global supply chain became disrupted and delivery times were increasing more and more by the end of 2021. "We had to move quickly in a short timeframe," Frank says.
On to a development path
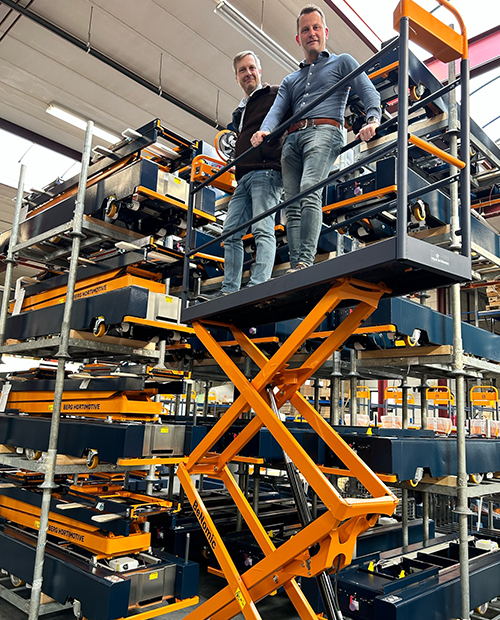
Frank consulted with his R&D colleagues. What are the alternatives? And if they are already available, how do we take care of integration, software and programming? To do all that in-house Berg Hortimotive did not have the capacity in the stipulated time of eight weeks. So, Frank discussed the possibilities with Ronald van Seters, key account manager at Panasonic Industry. Both already knew each other, as Panasonic components had been serving in tube rail cars for years. "But that was always on the basis of a customer-supplier relationship," Frank explains. "Now it was about a project-based approach. To have a development process in several areas."
In short, just supplying products was not enough. Instead, Panasonic Industry was asked to work together with Berg Hortimotive developing a new control system. Doing this deepened the cooperation, which is exactly what we like to do at Panasonic Industry, according to Ronald. "At our office in Best, it doesn't say People Before Products on the wall for nothing. Sure, good products are indispensable. But really distinguish yourself? You do that with your own people. They have the knowledge; they make the difference. That's the case here at Berg Hortimotive - and with us at Panasonic as well."
Matter of clear choices
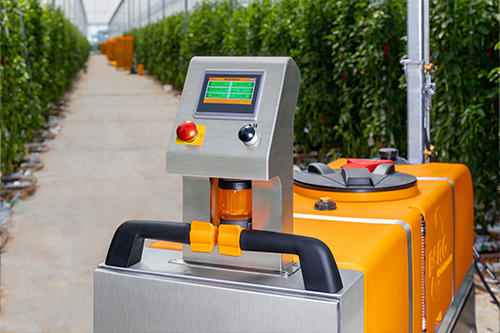
One such person is Roy Claessen, application engineer at Panasonic Industry and for this project the one who helped integrate the hardware, which includes several analogue modules in addition to a PLC and HMI display. Roy wrote the software and also helped access Corvina Cloud, allowing Berg Hortimotive to remotely log into a Meto robot's software, should the situation call for it.
That everything worked out so quickly, according to Roy, underlines the good cooperation with Berg Hortimotive. "And that had a lot to do with clear choices. For example, I started with a framework for writing the software. Basically, that it does what it needs to do, but gives room to add functionality during the process. That works better than making something very specific, after which practice turns out slightly different. If you make it too complicated at the start, it quickly becomes a time-consuming process."
A good preparation is half the battle.
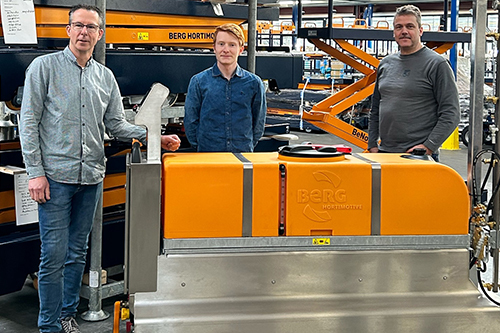
During the project, Roy worked closely with Stef Nibbelink, software engineer at Berg Hortimotive and his colleague Jaco Wessteijn, product developer and Meto control project leader. Both look back with satisfaction on the cooperation with Panasonic Industry. "Roy is an experienced engineer, who could quickly get to work with our input", Jaco says. "Anyway, that information had to be as clear as possible beforehand. So, we took care of that, especially considering the short period of eight weeks. The clearer our input, the greater the chance of success."
Stef agrees that such preparation takes time. "Still, it is good that we approached it this way. Optimal cooperation is only possible if you communicate well among yourselves. That is where the extensive documentation at the start of the project certainly helped."
Critical questions for optimisation
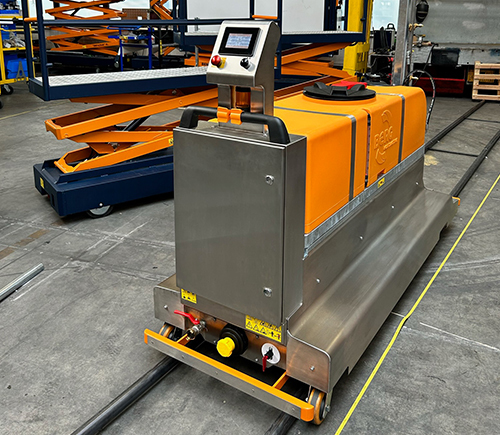
Furthermore, that thorough foundation offered another advantage, Jaco argues. "The first Meto was quite a while ago. That made the robot very natural for us, also in terms of the controls. So, it was valuable that Roy regularly asked us why we initially chose certain functions. Those critical questions also provided us with clear choices, and ultimately optimisation of the Meto control."
Take dynamic braking, for example. "The robot moves along the rails at a constant speed, but naturally has to brake as soon as it reaches the main path. Whereas this used to be at the same point every time, we now ensure that the robot automatically brakes later if the customer has chosen a lower speed. This prevents some plants from being sprayed too much. A nice addition."
Specialists speak each other's language
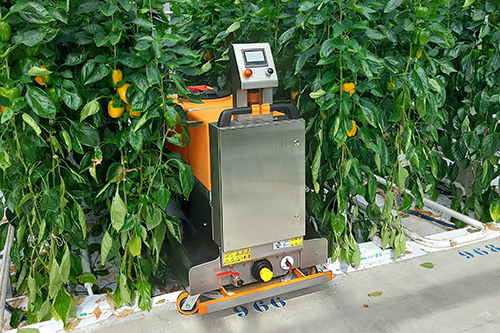
Dozens of Metos have already gone to customers with the new controls and the process, including subsequent optimisation, has ensured that the cooperation between both parties has strengthened. Roy has been very satisfied with the process. "Jaco and Stef are techies, just like me. That's pleasant working together. We speak each other's language, as do Frank and Ronald. Such a collaboration works well."
Speaking the same language and Panasonic Industry having a branch in Benelux, according to Frank, has certainly benefited Berg Hortimotive; "The whole process has been very smooth; besides, you are literally close by. And the fact that Panasonic realised everything with us in such a short time: that positively surprised me. The will to work it out together was there. In other words, not thinking in terms of impossibilities, but rather in terms of possibilities. This is exactly what we needed."
Harvest moment predicted
Berg Hortimotive's logistics solutions go to customers worldwide. More than sixty employees from De Lier, supported by a worldwide network of service partners, have automated processes in greenhouses and barns. Berg Hortimotive knows the power of data, as demonstrated by the Plantalyzer®. The tool helps growers predict the best time to harvest their crops and was developed under the HortiKey banner, in close cooperation with Wageningen UR and data company LetsGrow.com. Royal Brinkman - specialist for horticulture and owner of Berg Hortimotive since 2018 - is also one of the initiators of HortiKey.