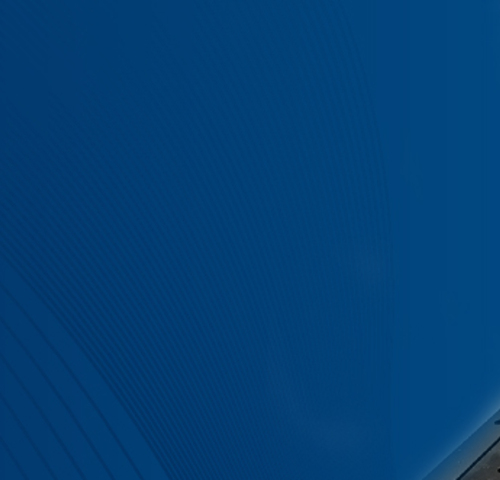
Marcado láser de piezas de acero inoxidable para maquinaria
En muchas industrias, es esencial marcar las piezas de las máquinas con números de referencia y, en algunos casos, con el tipo de material utilizado o el identificador de lote. Esto es especialmente crítico en el caso de los componentes de sistemas hidráulicos o de producción química que fabrica la empresa Tradeko, s. r. o. de Pelhřimov, República Checa. Con el fin de mejorar la productividad, Tradeko ha adquirido recientemente la estación de marcado láser LC 3000 de Panasonic Industry.
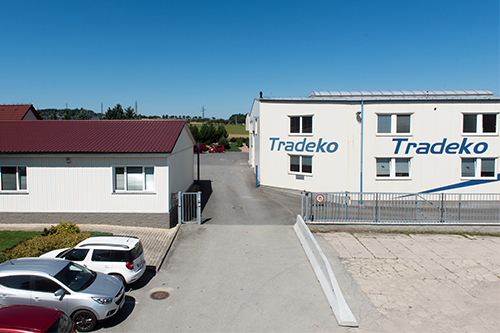
Tradeko, con sede en Pelhřimov, es un importante fabricante de resistencias eléctricas para radiadores de baño. Sin embargo, gran parte de su volumen de negocio se genera actualmente gracias a la producción de piezas mecanizadas a partir de aceros resistentes a la corrosión. La empresa cuenta con unas modernas instalaciones de mecanizado, que incluyen centros de torneado con husillos de fresado para piezas de 5 a 150 mm de diámetro. La mayoría de estas piezas son de acero 1.4571 (316Ti), adecuado para sistemas hidráulicos y para la industria química. Se utilizan aleaciones especiales de calidad marina para fabricar componentes destinados al sector de la construcción naval.
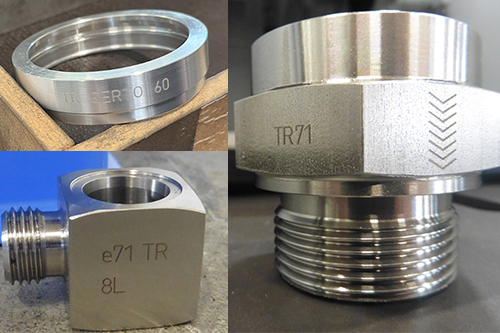
Todas las piezas fabricadas deben marcarse individualmente para especificar su tipo, fabricante y material. Los componentes para sistemas de presión también requieren el marcado del número de fusión del material. Ing. Zdeněk Lapáček, director general de Tradeko, explicaba: "Aproximadamente el 80% de las piezas que producimos requieren una identificación clara. Las exigencias de marcado son cada vez mayores, impulsadas por reglamentos, normas y requisitos de los clientes. El marcado de piezas pequeñas, con diámetros inferiores a 10 mm y longitudes inferiores a 15 mm, puede resultar complicado. Esta es una de las razones por la que decidimos adoptar el marcado láser; no hay muchas alternativas razonables".
El marcado se realiza con caracteres alfanuméricos para que resulten fácilmente legibles a simple vista (o con lupa), como se aprecia en las imágenes.
Anteriormente, Tradeko utilizaba dispositivos de micro impacto para el marcado. Este método consiste en crear pequeñas hendiduras en la superficie del material para formar los caracteres deseados. El principal inconveniente de este método es que requiere mucho tiempo. Cada pieza tenía que sujetarse a la máquina y girarse manualmente durante el proceso de marcado, sobre todo cuando se trabajaba sobre distintas superficies de materiales hexagonales o cilíndricos.
Para aumentar la productividad, Tradeko optó por invertir en la estación de marcado láser LC 3000.
Estación de marcado láser LC 3000
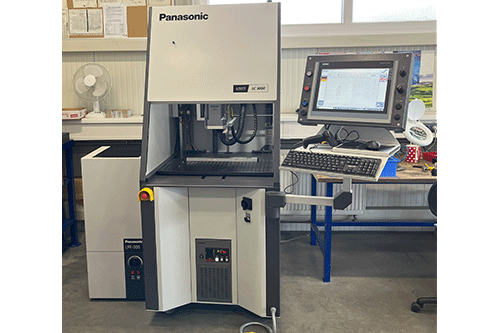
La estación de marcado láser LC 3000 es un equipo integrado que no solo lleva a cabo el proceso de marcado, sino que también garantiza la seguridad del procedimiento cuando se trabaja con radiación láser potencialmente peligrosa.
Estas estaciones de marcado son especialmente adecuadas para pequeñas y medianas empresas que fabrican una amplia gama de productos en lotes reducidos. Panasonic Industry ofrece diversas variantes con diferentes cabezales láser y configuraciones, lo que permite un alto grado de personalización para el marcado de productos específicos de plástico o metal.
Existen tres opciones de configuración fundamentales. La primera incluye movimientos en los tres ejes accionados por un servomotor, con un eje X de 500 mm, un eje Y de 430 mm y un eje Z de 350 mm. La segunda opción incluye un eje de rotación, y la tercera una mesa rotativa de 650 mm de diámetro.
Además del sistema de marcado láser, la placa de sujeción y los accionamientos, la estación de marcado LC 3000 incluye una cabina de seguridad con puertas servoaccionadas, una unidad de extracción de alto rendimiento, iluminación interna, un controlador lógico programable y un ordenador industrial con las aplicaciones de software necesarias para el marcado.
La elección del sistema láser dependerá del material y la geometría del marcado. Puede ser un láser de fibra (FAYb) para marcar plásticos y metales o un láser de CO2 para materiales orgánicos. Panasonic Industry ofrece una amplia gama de sistemas de marcado láser, desde 10 hasta 100 W, con un área de marcado de hasta 330 × 330 mm.
Una estación completa reduce costes y acorta el tiempo de puesta en marcha
¿Por qué eligió Tradeko la estación de marcado láser de Panasonic Industry? Zdeněk Lapáček comentó: «Una ventaja significativa para nosotros es que Panasonic Industry nos proporciona una estación de marcado completa que incluye elementos de seguridad, una unidad de extracción y un ordenador industrial para programar el proceso de marcado. Recibimos ofertas de la competencia, pero solo ofrecían el láser en sí. Habríamos tenido que diseñar y construir el resto de la estación de trabajo o buscar otra empresa que lo hiciera, lo que habría aumentado los costes y retrasado la puesta en marcha. En este caso, basta con configurar la estación de marcado LC 3000 según el tipo de piezas que se desee marcar y suministrarla al cliente. Kipex, la empresa que nos ayudó a instalar la estación, también nos proporcionó formación y asesoramiento, y ahora es la encargada de realizar todas las tareas de mantenimiento necesarias. Lo único que añadimos nosotros fue un pedal de control, elemento al que nuestros operarios ya estaban habituados gracias a las estaciones de micro impacto.»
Marcado 2D vs. Marcado 3D
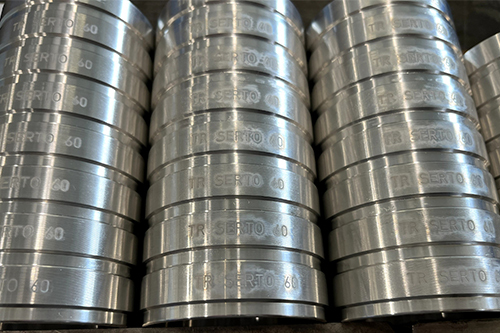
La estación LC 3000 de Tradeko está equipada con un sistema de marcado láser 3D que emplea un láser de fibra (FAYb LP-Z250). Se trata de un sistema de marcado láser 3D que permite realizar marcas en superficies inclinadas, convexas y cóncavas en un rango de altura de 50 mm gracias al control del eje Z. Dentro de este rango, el tamaño del láser se mantiene estable, lo que garantiza un marcado uniforme y de alta calidad. En combinación con una gran área de trabajo (120 × 120 mm), permite marcar sobre formas complejas sin perder calidad de grabado en los bordes.
Según Zdeněk Lapáček, la capacidad de marcado en 3D es vital para esta aplicación: «En el caso de sistemas 2D más sencillos, habríamos tenido que marcar cada componente por separado. Comparado con el marcado por micro impacto, esto no nos habría ahorrado tiempo, sino todo lo contrario.»
Tradeko marca las piezas mediante grabado láser. Aunque los láseres también pueden marcar la superficie del acero mediante recocido (cambiando su color sin eliminar material), este método no era el más adecuado para esta aplicación. En los entornos extremos en los que se utilizan a menudo estas piezas, el marcado podría volverse ilegible rápidamente debido al desgaste.
Sin embargo, el grabado tiene un inconveniente: el material eliminado de la pieza marcada se dispersa en el entorno y puede acumularse en la lente del láser. Esto reduce la calidad del marcado, lo que obliga a limpiar regularmente la lente. Para minimizar este problema, la estación LC 3000 está equipada con un potente sistema de extracción. Utiliza principalmente la unidad LFE-275 con un caudal de extracción nominal de 80 m3/h a 1.900 Pa. Se pueden utilizar unidades externas más potentes de forma opcional. Además de eliminar los residuos de la zona de trabajo, la unidad también evita la dispersión del material en el entorno. De este modo, lo único que hay que limpiar después de cada operación de marcado es la superficie de las piezas, la cual puede acumular pequeños depósitos alrededor de la zona de marcado.
Una programación simplificada facilita su uso en la producción de lotes pequeños
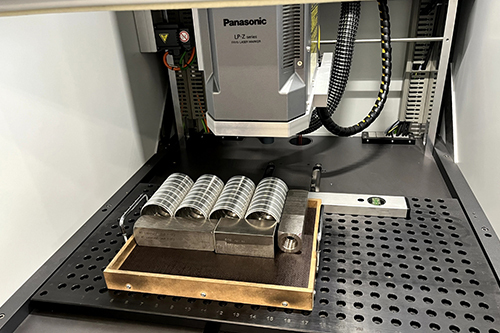
Al principio, a Zdeněk Lapáček le preocupaba el tiempo que llevaría configurar, ajustar y programar la estación láser. La programación del marcado en 3D es más compleja que la del marcado en 2D, por lo que quería poder preparar los programas con antelación basándose en planos CAD. Aunque el software lo admite, resultó innecesario. Comentó: "Me preocupaba pasar más tiempo configurando que marcando. Quería tener listos de antemano nuestros programas de marcado para ahorrar tiempo. Sin embargo, mis colegas, que aprendieron a trabajar con el software, me convencieron de que crear programas de marcado es tan fácil y rápido que no es necesaria ninguna preparación. Se trata esencialmente de familiarizarse con el software instalado en el ordenador industrial. Éste permite configurar todo lo necesario: el contenido del marcado, la ubicación, el ángulo o el radio de la superficie de marcado, así como otros parámetros. Eso es todo. Tras un breve curso de formación, la configuración es rápida.»
En el ordenador industrial, parte integrante de la estación de marcado LC 3000, está instalado el software Laser Marker NAVI Plus. Cuenta con una interfaz fácil de usar que simplifica la configuración del marcado y facilita la planificación y la creación de diseños. El software también permite supervisar el funcionamiento del sistema, comprobar los registros de errores y controlar los estados de entrada y salida. Las aplicaciones Logo Data Conversion y Logo Data Editing están diseñadas para trabajos gráficos.
Retorno de la inversión
Actualmente, Tradeko marca hasta 5.000 piezas mecanizadas al día. Para ello, utilizan una estación de marcado láser LC 3000 y dos de las cuatro estaciones de marcado por micro impacto semiautomáticas. El marcado por micro impacto se utiliza principalmente como opción de reserva o cuando el marcado por láser no resulta adecuado, por ejemplo, cuando el cliente aplica un revestimiento para el que el marcado láser es demasiado superficial y no resultaría legible.
Cuando se le preguntó por la rentabilidad de la inversión en la estación LC 3000, Zdeněk Lapáček respondió: "La estación de marcado láser 3D cuesta casi diez veces más que la estación de micro impacto, por lo que hay que sopesar bien la inversión". Calcular el rendimiento exacto es un reto para nosotros ya que nuestra producción es muy diversa, y el marcado láser no se utiliza para todas las piezas. Sin embargo, estimo que la inversión se amortizará en cinco años. La gran ventaja del marcado láser 3D es la posibilidad de marcar muchas piezas al mismo tiempo, lo que aumenta considerablemente la productividad. Sin esta capacidad, el marcado láser sería un reto para nosotros.» También valora muy positivamente la colaboración con Kipex, que ayudó a Tradeko con la puesta en marcha de la estación y la formación de los operarios y que ahora presta servicios de mantenimiento.
(Gracias a Ing. Zdeněk Lapáček, director general de Tradeko, s. r. o. y a Ing. Stanislav Hanka, de Kipex s. r. o., por la información facilitada).
Petr Bartošík, adaptado de la revista Automa, 5/2023.