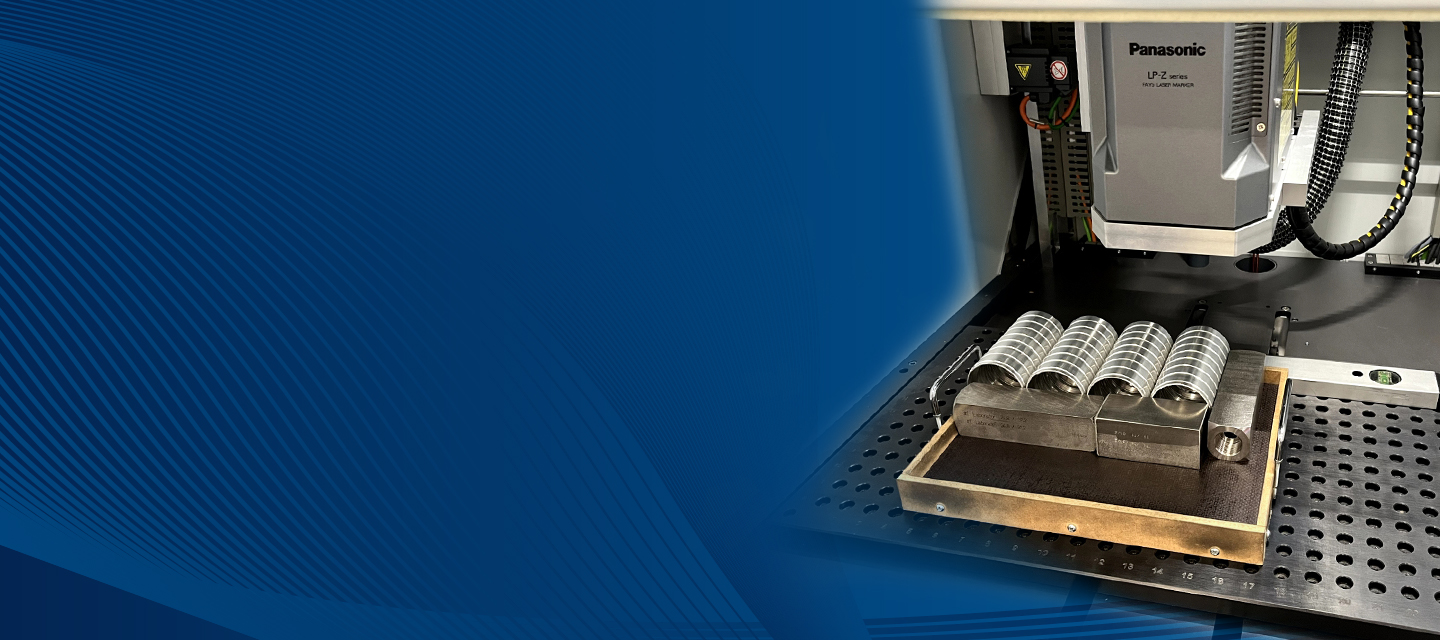
Laser Marking of Stainless-Steel Machine Parts
In many industries, it is essential to mark machine parts with item numbers and, in some cases, the type of material used or the product batch identifier. This is particularly critical for components in hydraulic systems or chemical production, which are manufactured by the company Tradeko, s. r. o. from Pelhřimov, Czech Republic. In order to enhance production efficiency, Tradeko has recently acquired the LC 3000 laser marking station from Panasonic Industry.
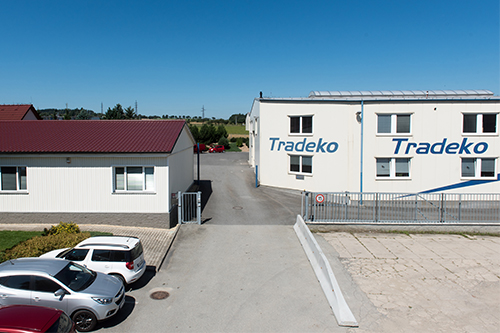
Tradeko, headquartered in Pelhřimov, is widely recognized for manufacturing electric heating elements for bathroom radiators. However, the majority of its turnover is currently generated by producing machined machine parts from corrosion-resistant steels. The company boasts a modern machining facility, including turning centers with milling spindles for components ranging from 5 to 150 mm in diameter. Most of these parts are made from 1.4571 steel (316Ti), which is suitable for hydraulic systems and the chemical industry. Special marine-grade alloys are used to produce components for the shipbuilding sector.
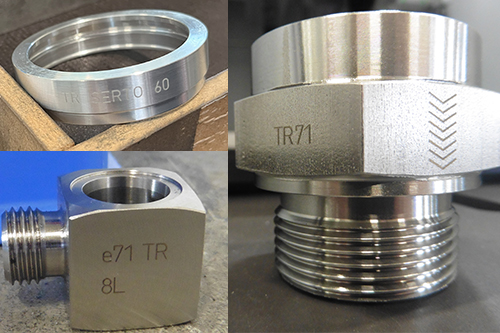
All manufactured parts need to be individually marked to specify their type, manufacturer, and material. Components for pressure systems also require the marking of the material melt number. Ing. Zdeněk Lapáček, Tradeko's Managing Director, explained, "Approximately 80% of the parts we produce require clear identification. The demands for marking are increasing, driven by regulations, standards, and customer requirements. Marking on small parts, with diameters under 10 mm and lengths under 15 mm, can be challenging. This is one of the reasons why we decided to adopt laser marking; there aren't many reasonable alternatives."
The marking is done with alphanumeric characters to ensure that it is easily legible to the naked eye (or under magnification), as seen in the pictures.
Tradeko previously used micro-impact devices for marking. This method involves creating small dimples on the material's surface to form the desired characters. The primary drawback of this method is its time-consuming nature. Each part had to be clamped into the machine and manually rotated during the marking process, especially when marking on various surfaces of hexagonal or cylindrical materials.
To enhance productivity, Tradeko opted to invest in the LC 3000 laser marking station.
The LC 3000 Laser Marking Workstation
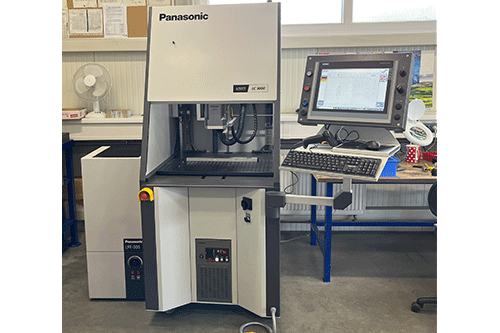
The LC 3000 laser marking workstation is an integrated workstation that not only carries out the marking process but also ensures the safety of the procedure when working with potentially hazardous laser radiation.
These stations are particularly well-suited for small and medium-sized enterprises that produce a wide range of products in small batches. Panasonic Industry offers several variants with different laser heads and configurations, allowing customization for marking specific plastic or metal products.
Three fundamental configuration options are available. The first includes three-axis servo-motor-driven movements, with a 500 mm X-axis, 430 mm Y-axis, and 350 mm Z-axis. The second option includes a rotary axis, and the third features a rotary indexing table with a 650 mm diameter.
In addition to the laser marking system, clamping plate, and drives, the LC 3000 workstation includes a safety cabin with servo-driven doors, a high-performance extraction unit, internal lighting, a programmable logic controller, and an industrial computer with the necessary software applications for marking.
The choice of laser system depends on the material and geometry of the marking. It can be a fiber laser (FAYb) for marking plastics and metals or a CO2 laser for organic materials. Panasonic Industry offers a wide range of laser marking systems, ranging from 10 to 100 W, with a marking area of up to 330 × 330 mm.
A Comprehensive Station Reduces Costs and Shortens Commissioning Time
Why did Tradeko choose the Panasonic Industry station for laser marking? Zdeněk Lapáček explained, "One significant advantage for us is that Panasonic Industry provides a complete workstation, including safety features, an extraction unit, and an industrial computer for programming the marking process. We received offers from competitors, but they only offered the laser itself. We would have had to design and build the rest of the workstation or find another company to do it, which would have increased costs and extended the commissioning time. Configuring the LC 3000 workstation is sufficient, based on the type of parts we want to mark, and it is delivered to the customer as a whole. Kipex, the company that helped us set up the station, provided training and consultations and now provides servicing. The only thing we added was a foot pedal control, which our operators were already familiar with from the micro-impact stations."
2D Marking vs. 3D Marking
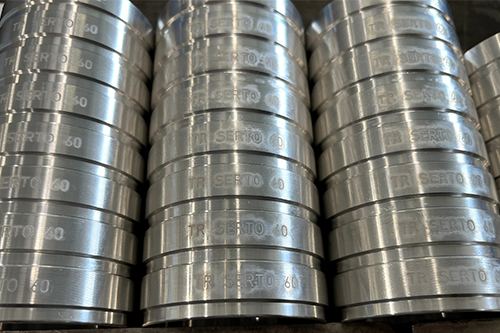
The LC 3000 workstation in Tradeko is equipped with a 3D laser marking system using a fiber laser (FAYb LP-Z250). It's a 3D laser marking system, which allows marking on inclined, convex, and concave surfaces in a height range of 50 mm due to control of the Z-axis. Within this range, the size of the laser spot remains stable, ensuring consistent and high-quality marking. Combined with a large working area (120 × 120 mm), this enables marking on complex shapes without any loss of marking quality on the edges.
According to Zdeněk Lapáček, the 3D marking capability is vital for this application: "For simpler 2D systems, we would have had to mark each component individually. Compared to micro-impact marking, this would not have saved us any time; quite the opposite."
Tradeko marks parts using laser engraving. Although lasers can also mark by annealing the steel's surface, changing its color without material removal, this approach was not suitable for this application. In harsh environments where these parts are often used, the marking could quickly become illegible due to wear and tear.
However, engraving has a drawback: material removed from the marked part scatters into the environment and can accumulate on the laser's lens. This reduces marking quality, necessitating regular cleaning of the lens. To minimize this, the LC 3000 workstation is equipped with a powerful extraction system. It mainly uses the LFE-275 unit with a nominal flow rate of 80 m3/h at 1,900 Pa, or optionally more powerful external units. Besides removing residue from the working area, the unit also prevents material dispersion into the surrounding environment. As a result, the only thing that needs cleaning after each marking is the surface of the marked parts, which may accumulate slight deposits around the marking area.
Simplified Programming Facilitates Use in Small-Batch Production
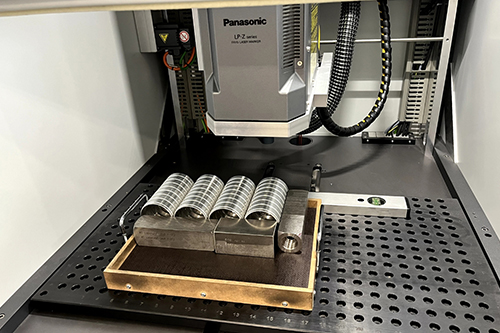
Zdeněk Lapáček was initially concerned about the time it would take for setup, adjustment, and programming of the laser station. Programming 3D marking is more complex than 2D marking, so he wanted to be able to prepare programs in advance based on CAD drawings. While the software supports this, it turned out to be unnecessary. He explained, "I was concerned about spending more time setting up than marking. I wanted to have our marking programs ready in advance to save time. However, my colleagues, who learned to work with the software, convinced me that creating marking programs is so easy and quick that no preparation is needed. It's essentially about becoming proficient with the software installed on the industrial computer. It enables setting everything necessary: the marking content, location, angle or radius of the marking surface, and several other parameters. That's it. After a short training, the configuration is swift."
On the industrial computer, an integral part of the LC 3000 workstation, the software Laser Marker NAVI Plus is installed. It offers a user-friendly interface that simplifies marking configuration and facilitates easy planning and layout creation. The software also allows monitoring system operation, checking error logs, and monitoring input and output statuses. Logo Data Conversion and Logo Data Editing applications are designed for graphic work.
Return on Investment
Currently, Tradeko marks up to 5,000 machined parts daily. To achieve this, they use one LC 3000 laser marking station and two out of four semi-automatic micro-impact marking stations. Micro-impact marking is primarily used as a backup option or when laser marking is not suitable, for instance, when the customer applies a coating for which laser marking is too shallow and would not be legible.
When asked about the return on investment for the LC 3000 station, Zdeněk Lapáček responded, "The 3D laser marking station costs nearly ten times as much as the micro-impact station, so the investment needs to be carefully considered. Calculating the exact return is challenging for us because our production is highly diverse, and laser marking is not utilized for all parts. However, I estimate that the investment will pay off within five years. The significant advantage of 3D laser marking is the ability to mark many parts simultaneously, significantly boosting productivity. Without this capability, laser marking would be challenging for us." He also highly values the collaboration with Kipex, which assisted Tradeko with station commissioning, operator training, and now provides servicing.
(Thank you to Ing. Zdeněk Lapáček, Managing Director of Tradeko, s. r. o., and Ing. Stanislav Hanka of Kipex s. r. o. for provided information)
Petr Bartošík, Adapted from Automa magazine, 5/2023.